上汽大众MEB工厂是近年来建成投产的一家现代化工厂,坐落在上海安亭,建有冲压车间、焊装车间、涂装车间、动力电池组装车间、汽车总装车间,专为生产大众MEB平台车型,总投资约170亿元,规划年产能30万辆。采用大众集团全球最先进的数字化生产技术,生产线上共有1400多台机器人,自动化程度高,实现了工业无线网络全覆盖,新工厂是上汽大众面前最先进、最智能的标杆工厂。本期为大家介绍MEB工厂焊装线的主要亮点。
亮点一:物流优先的平面布局。焊装车间就是把各个零件拼接成白车身的地方,车间分两层,一楼是门盖、底板1线和装配线,二楼主要是侧围、底板2线、总拼以及报交线。
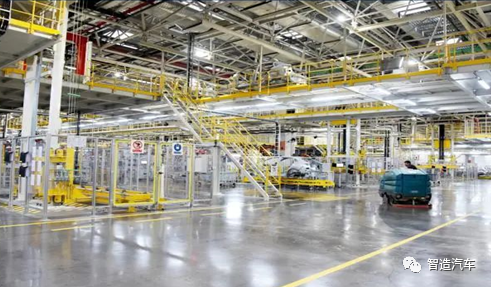
亮点二:焊接自动化程度创新高。目前焊装车间的设计生产节拍为60JPH,按年5000小时计算的产能为30万台白车身,车间机器人数量为946台,自动化率达到84%,这是上汽大众自动化率最高的焊装车间。上汽大众MEB工厂焊装自动化率采用的计算方法,是按机器人数量除以工人和机器人数量之和来进行计算的。其它公司的焊装工厂焊装自动化率计算方法可能不尽相同,自动化率可能存在差异,不能进行简单的横向对比。自动化程度高,产品质量的稳定性和一致性能得到更好的保证,与此同时,对质量管理和控制要求也更高了,因为一旦出现焊接质量问题,就一定是批量的,因此需要从工艺源头和自动检测、预测分析等方面加强焊接质量的管控。
焊装线上采用的机器人全部是KUKA品牌,每台机器人上都有一个小仪表,这是一个压力表,用来监控机器人是否出现异常。
焊装车间有不同的分焊线,例如车门、侧围、底板、两盖等分总成焊接线,焊接工艺大同小异。亮点三:柔性化的总拼焊接系统。上汽大众自主开发、自主享有知识产权的白车身柔性总拼焊接系统,可支持6种车型生产,最高可扩展至8种,为未来不同品牌、车型的生产奠定了基础。这套总拼焊接系统不仅柔性化水平高,而且焊装尺寸精度高。
亮点四:采用车身定位雪橇技术。生产线中应用了定位雪橇,它与传统雪橇相比较,增加了底部夹紧机构,可将车身固定在雪橇上,在补焊线焊接时无需升降滚床和底部夹具,可以提升节拍,优化空间。
亮点五:首次采用机器人全自动拧紧工艺。车间同时应用了许多前沿技术,包括首次采用机器人全自动拧紧工艺,进一步提升自动化水平,自动拧紧工位见下图所示。
车间共有两个自动拧紧工位,含有12台机器人,平均每台机器人拧两个螺栓,拧紧时间大约40秒,如果加上车身在工位之间运行时间,整个节拍为51秒。
它针对不同的工况选取不同的技术方案,自主开发螺栓送、取钉技术,拧紧的步骤包括取钉、初拧紧、预拧紧、中拧紧再到终拧紧,每次拧紧的扭矩都不一样,其中终拧紧力矩为59N.m。
据了解,工厂进行了1000多次取钉试验,做到无故障发生,同时克服了无技术标准的困难,保证生产过程稳定进行。亮点六:首次采用了冷金属过渡焊接工艺。焊接工艺方面,首次采用CMT+工艺,全称叫做冷金属过渡焊接,与传统焊接工艺比较,过度焊接熔滴温度相对较低,零件热变形小。焊接过程可达每分钟70次的抽拉丝速度,并且不产生飞溅 ,不受工件表面状态影响,能使焊缝的成型更美观。
与此同时,它采用了高密度补焊,可适用不同车型,无需切换焊枪,焊接能力提升3倍。负责该工序现有14台焊接机器人,未来可扩展到16台。
亮点七:高速激光焊工艺技术。在焊接完车顶和侧位后,车身就准备进入激光焊工位。这个工位包含激光焊和几个焊点的补焊。采用的激光焊的焊接速度可达110mm/s,是大众汽车集团工厂中速度最快的激光焊,提高速度可以更好地满足产能的需求。总体节拍还是51秒,焊接过程基本在40秒左右。
激光焊的优势包含高功率密度、优良的方向性和高焊接速度,焊缝表面光洁。它可替代车顶和侧围连接的焊点,也无需在车顶安装密封胶条,同时可精确调节和控制热输入,镀锌层烧损更少,减小焊件的变形。亮点八:采用机器人自动打磨工艺。激光焊之后是机器人自动打磨和人工打磨工位,其中工人主要检查机器人的打磨质量,如发现哪里打磨得不好,再简单整理一下。
亮点九:机器人视觉在线检测焊接质量。在整条总拼线,最不能错过的是At-line测量工位,它是大众汽车集团全球首个At-line测量工位,由8台测量机器人对白车身的几何尺寸和关键部位实现100%的视觉在线检查。与传统测量工位需要将被检车辆从生产线上运输到测量间相比,在线测量将工位串联在生产线中,可直接在生产线上抽取车辆进行检查,有效节省运输时间提高检测效率(最快只需7分钟完成车身扫描),同样也提升了检测数量。At-line同时实现了云端数据核对,在线检测结果传输到质保控制室,发布到系统中,技术员可以网上直接看到质量状态,及时跟踪优化,保证了白车身生产制造过程的稳定性。
亮点十:高效的四门两盖装配地面输送线。完成At-line测量后,接下来是安装四门两盖、翼子板覆盖件,上汽大众最长的焊装车间装配线,长达150米,装配线配备了随行皮带,能减轻了工人一半的走动距离,降低了劳动强度。
亮点十一:EMS空中输送存储线。四门两盖都是空中输送下来的,这是因为车间首次采用了EMS空中输送存储线,它总成6000米,空中最多可存储180套门盖总成,能实现6种车型识别和搬运功能。传统操作需要使用牵引车或AGV小车输送四门两盖,并需要专门空间存储零件,采用EMS空中输送后将零件存储于空中,节约地面空间,优势很明显。
在完成四门两盖安装后,车身就会送去检测,如果确认符合要求,白车身才能进入涂装车间。总之上汽大众MEB工厂焊装车间的建设汇集了上汽和大众两家公司的优质资源,生产线亮点纷呈,柔性化自动生产程度高,物流顺畅,工艺先进,技术一流,质量控制严格,不仅是国内汽车制造届学习的榜样,也是我们研究车身焊装智能化制造发展趋势的经典案例。在在数字化转型升级阶段,如何分类采集焊装的制造数据、如何建立数学模型、如何利用工业大数据平台对车身焊接质量进行分析预测、预控,防止产生不合格车身,尤其是要预防出现批量不合格车身。来源:智造汽车 汽车之家