《新能源汽车产业发展规划(2021~2035年)》国家战略性发展规划报告中,更加明确了我国未来新能源汽车的重要战略地位,从而国内乘用车的开发也越来越重视车身轻量化、碰撞安全性,行驶经济性等功能需求。加之世界车身金属材料工艺发展的愈发成熟,高强度钢板在白车身结构上运用的更加普及。
为实现而这些功能需求,当前国际主流则是采用热成型工艺,但是其开发工艺复杂、制造成本高以及二次成型及翻边整形相当困难的特性,也迫使冷冲超高强钢板的大量应用已经普遍存在,将冷冲高强度钢用于侧围总成框架上,不仅满足车身骨架结构强度和刚度的同时减轻了重量,更是大大保证了行驶仓内乘员的安全性。
然而冷冲高强板具有屈服应力大、抗拉强度高、延伸率低、成型力量大、成型性能弱、以及硬化指数n值和厚向异性系数r值低的复杂特性,也使得其在冷冲压成型过程中非常容易产生更大的弹性应变,造成制件开裂、回弹、扭曲的质量风险也愈发突出。
为确保制件的高精度要求,整个产品开发工艺环节需要在产品设计、冲压SE开发、造型优化、成型数值模拟分析、工艺合理排布、模具结构优化、工艺参数设置、现场维修整改调试以及潜在性失效模式识别等众多方面进行细化分析。
而本文也正是重点通过QP980中支柱里板高强板成形工艺开发及制件回弹整改典型案例进行了系统的分析和探讨研究,为车身高强板冷成形产品开发提供了宝贵的指导和借鉴经验。
产品研究背景
产品装车环境
中立柱里板属于汽车白车身框架重要零件,上部小端头主要连接A柱骨架总成,下部大端头连接门槛总成,中部法兰区域与热成形高强钢中立柱点焊无缝搭接,因此对其强度、刚度及焊接尺寸都有极其严格的工艺要求,而目前该类“弧形”里板类零件大多数采用屈服强度≤590材质拉延成型,超过该屈服强度几乎均采用热成型+镭射切割工艺方案。而此次研究探讨对象为某车型中立柱里板冷成型生产工艺,其零件材质为QP980超高强钢板,料厚为1.2±0.13mm。
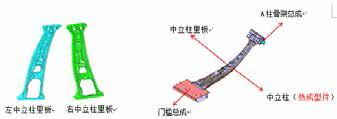
材料力学性能
QP980钢板作为为第三代超高强钢,是一种高强度高塑(韧)性的马氏体钢(也成淬火延性钢),钢材韧塑性、成型性和延伸凸缘性等显著提高。其各主要化学元素含量如表1,通常可以达到的力学性能范围为:抗拉强度800~1500MPa,屈服强度达550~1100MPa,延伸率15%~40%,较宽范围的力学性能虽然为汽车钣金成型材料牌号提供了多种选择余地,但另一方面也大大增加了冷成型模具开发及调试整改难度。
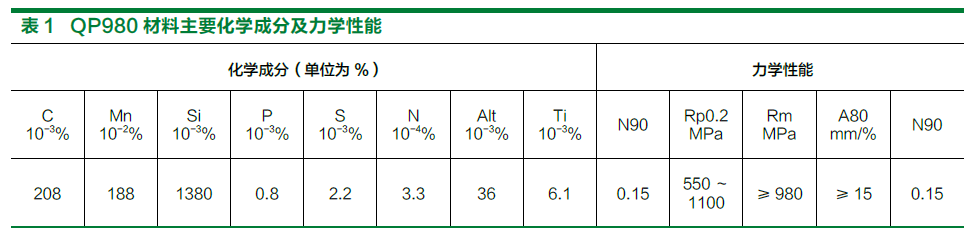
为了让CAE模拟分析更加准确有效,使用单项拉伸机对宝武钢QP980材质进行实验测试,以便获得板材的基本力学性能,拉伸试样如图1图2所示,实验时变形的速率约为0.005S,其结果为:抗拉强度1100MPa,屈服强度820MPa,断后延伸率在16%以上,基本与后面分析材质参数一致。
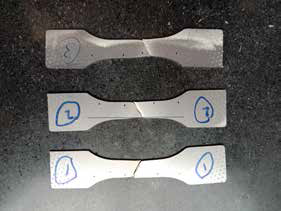
图1 拉伸试片
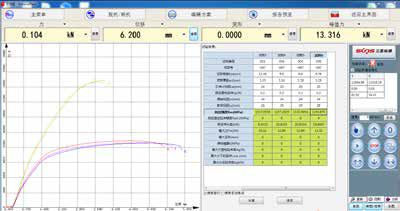
图2 拉伸曲线
产品成型特点
该零件尺寸为:1190mm×340mm×115mm,整个零件有反拉延造型且呈“弓”形,23处冲孔,2处翻孔,单件净重1.856Kg。目前采用4道生产工序完成,其分别为:OP10拉延、OP20修边冲孔、OP30修边冲孔吊冲孔、OP40“双活”翻边整形。产品拉延深度为120mm,成型力要求达到1150T左右,四周法兰面差尺寸公差要求在±0.4mm之内,翻孔面角度要求为80°修边线尺寸公差要求在±0.4mm之内,因此对法兰面回弹进行有效的分析和控制是保证该产品合格的关键所在。
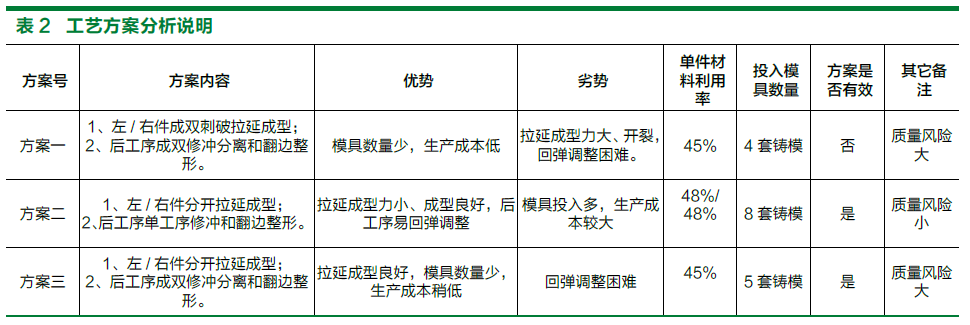
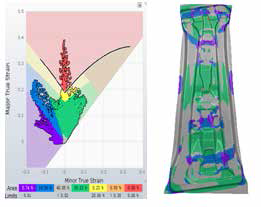
图3 单件拉延成型云图
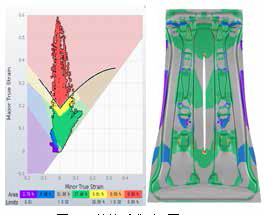
图4 双件拉延成型云图
工艺方案分析
拉延成型数值模拟初步分析
通过以上初步CAE分析结果及成形过程可以看出,零件分开拉延成型(图3)理论成型力720T基本无较大开裂,产品区域最大减薄率为12%左右,冲孔废料区起皱最大0.04mm,其它范围趋势可接受。而零件双拼理论形型力达1400T,采用不太常用的刺破拉延成型(图4)方式依然存在较大开裂趋势,材料开裂和刺破后起皱趋势同样较为明显,后期SOP阶段存在很大生产质量风险且双件回弹比单件更难控制。
正式工艺排布
通过以上工艺方案分析说明,且考虑到超高强板零件成型力量巨大,冲裁噪声明显,回弹调试整改繁杂等方面,则采用相对保守有效的方案二冲压工艺制造该对零件,其工艺方案排布为:M01开卷摆剪——OP10拉延——OP20修边冲孔吊冲孔——OP30修边冲孔吊冲孔——OP40“双活”翻边整形翻孔,具体内容如图4所示。
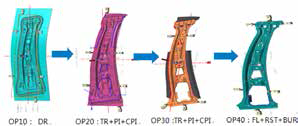
图4
正式工艺CAE全工序仿真模拟
为更好优化验证该冲压工艺方案的合理性,采用AotuformR7软件膜单元FV精度级别对其进行全工序含回弹仿真计算模拟。模拟参数及评判边界条件分别为:成形减薄率≤16%,压边圈区域最大起皱≤0.05mm,凸模区域≤0.03mm,摩擦系数0.15并采用自由回弹方式分析回弹。
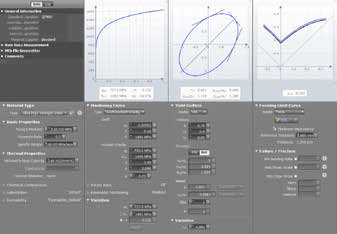
图5
根据图5材质参数卡:分析选用宝武钢QP980材质,屈服强度Rp0.2为737.5MPa,抗拉强度Rm为1082MPa,屈强比为0.682,断后延伸率A80mm为16.3%,应变硬化指数n值为0.152。
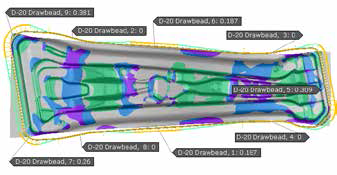
图6 OP10 拉延3D 实体筋布置
OP10拉延3D实体阻力筋设置分布情况:整体拉延圆筋半径R8mm,仿照分模线外移扩大15mm布置,共分为9段方便局部阻力调整。其中筋2、筋3、筋4和筋8因流料需要阻力系数设置为0,筋5、筋7和筋9因需控制两端头走料和回弹阻力系数设置分别为0.309(547N/mm)、0.260(461N/mm)和0.381(674N/mm),筋1和筋6因需控制中间法兰面走料和回弹阻力系数设置为0.187(331.0N/mm)。
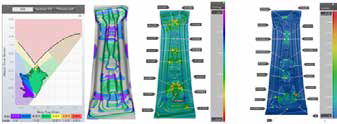
图7 拉延结束FLD 图 图8 拉延减薄率云图 图9 拉延起皱云图
OP10拉延结束FLD结果:成型力理论812T,压边力理论120T,大减薄率为13%,产品面区起皱最大0.04mm。
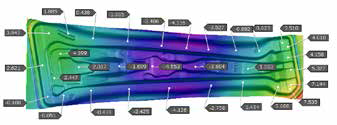
图10 OP10 拉延回弹云图
OP10拉延结束回弹结果:非常产品区域向上最大+7.5mm,产品区域向下最大-4.5mm。
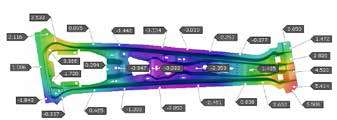
图11 OP20/30 修边回弹云图
两序修冲结束回弹结果:产品区域向上最大+5.5mm,向下最大-3.2mm。
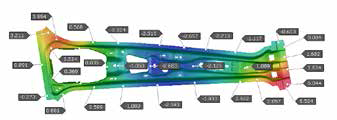
图12 OP40 翻边整形回弹云图
OP40翻边整形结束回弹结果:产品区域向上最大7.28mm,向下最大-3.9mm。
实际分析过程中拉延开裂和起皱现象并存,采用先优化起皱再优化开裂的顺序,对其OP10拉延筋位置、形状、大小、模面工艺补充面形状和进料圆角大小、压边力以及板料尺寸、位置和定位反复进行优化调整试验。
为了更好控制材料流动速度和抑制回弹量,没有直接选择产品四周法兰面作为压料面,而是直接外延增加工艺补充,促使成型过程中材料被充分拉开硬化。当OP20/OP30修冲结束后,产品局部位置因失去废料,拉/压应力迅速释放造成回弹发生明显趋势和量变化。
OP40翻边整形工艺对前工序回弹矫正作用不是非常明显,局部回弹位置反而有变严重趋势,成品回弹远远超过了产品GD&T中±0.4mm的要求,不能用于指导模具制造和调试,基于回弹结果必须进行逐步反向补偿优化至±1.0mm以内方可进行开模。
同时这些回弹趋势变化表明下步模面设计过程中需要充分考虑全工序回弹补偿,将回弹补偿量合理分配到各个工序中去、型面镶块需要分块增厚便于型面多次降刀加工等,为后期回弹整改提供便捷。
模具结构设计
该材质为超高强板OP10拉延模模座主筋壁厚采用50mm且随分模线靠内侧凸模受力部位均匀布置,压边圈采用内角导向,120T压边力采用21根锥形顶杆腿支撑传递液压垫压力。另外考虑到该模面后期需要进行多伦回弹补偿加工,凹模和凸模首先采用MoCr合金铸铁分块镶块,待后面完成多伦回弹补偿加工整改面差在±1.0mm模面之内且处于稳定状态后,方可进行改用Cr12MoV硬料镶块。压边圈压料面在回弹整改加工内容比较少,则直接采用分块Cr12MoV硬料镶块研配合模,如此可以在模具整改加工效率和制造成本两方面上取得一个很好的平衡点。
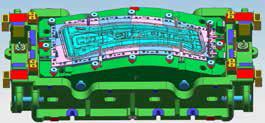
图13 OP10 拉延模下模结构
OP20和OP30工序内容为四周共6段分切正修边,OP20中间冲两大异形孔,正冲11小孔,小端头φ12.2圆孔与冲压方向存在70°夹角;OP30中部孔与冲压方向存在73°夹角,为保证这些孔形状与产品数模一样,则只能采用在压料芯内部埋入吊斜暗冲孔。OP20小端头修边与冲压方向存在64°修边夹角,OP30大端头修边与冲压方向存在78°修边夹角,上模压料芯和修边刀块在压料冲裁过程中存在较大的侧向力,因此在下模对应位置特意各增加了3处反侧导板,保证压料芯和上模在下行工作时,提前进行导向反侧,以便提高修边质量和模具使用寿命。
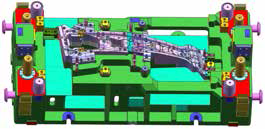
图14 OP20 修边冲孔吊冲孔下模结构

图15 OP30 修边冲孔吊冲孔下模结构
OP40工序内容为上/下翻边、翻孔和四周法兰焊接面整形,采用传统“双活”结构,先进行上翻边和翻孔再进行下翻边,由于既要完成翻边压料/托料又要完成整形,部分整形面只能分在下模托料芯上,因此上模压料芯和下模托料芯均需要在模具闭合时处于墩死状态。另外在整形过程中上压料芯同样受到较大侧向力,故也在下模适当位置增加3处反侧导板,以提高整形模工作的稳定性。

图16 OP40 翻边整形下模结构
模具调试整改
工艺分析和模具设计阶段通过一系列反复回弹补偿分析,结构上也是重点对可能出现的回弹面进行预防控制,首次出件状态如图17所示。

图17
左/右中支柱里板超高强冷成型零件首次出件回弹趋势基本与工艺设计分析结果一致,零件整体两端头呈现向凸侧外张下榻扭曲现象(图17红色与蓝色区域),中部则是向凹侧内凸现象,只有介于中部与端头之间部分位置区域才能与产品数据拟合一致(图17绿色区域),实物左件单向回弹值最大为+1.8mm/-1.0mm,双向极差达2.8mm,实物右件单向回弹值最大为+1.3mm/-1.6mm,双向极差达2.9mm。
分析出现这些问题原因主要可能有:①模拟分析过程中材料参数设定与实际调试材料存在一定的差别;②有限元建模采用的是刚性模面,实际模面在受力成形过程会存在微观变形;③模具实物加工型面与数字模型无法完全做到一模一样;④现场调试人员选择调试参数与理论计算有差别;⑤模面研合率及粗糙度与分析过程中存在一定偏差;⑥现场设备精度失真造成调试压力设置错误;⑦生产过程退料造成工序产品变形;⑧检具夹钳位置与回弹分析夹持点存在位置和力量偏差;⑨零件码放重力造成部分位置受力变形;⑩检具错误和三次元等检测工具精度失真也会造成测量结果显示错误。
而在实际整改过程中则需要对这些影响因素进行单项试验分析识别与排除,如此才能制定的出行之有效的方案。
现场回弹常用整改方法与流程
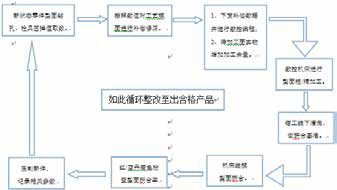
制件实际回弹补偿量与实调结果(以左件举例)
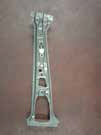
图18 左中支柱里板实物图
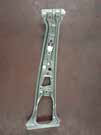
图19 右中支柱里板实物图
最终制件关键位置测量状态显示如下:
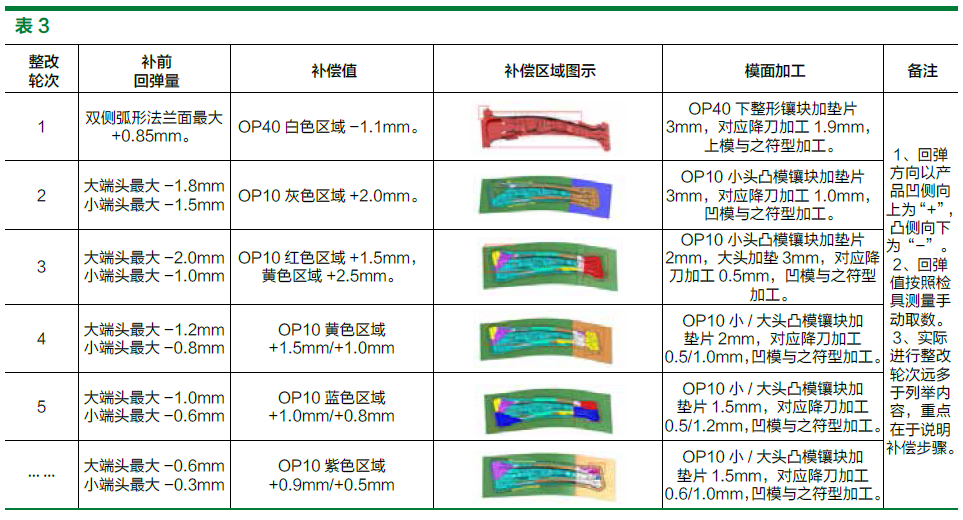
持续数月轮番补偿整改后,左/右件型面检测点面差值基本已落在公差要求范围之内,左件超差最大位置在小端头,最大值为-0.9mm,右件超差最大位置在大端头,最大值为-0.8mm。当前针对这些局部超差点采用的是“少量多次”补偿整改策略,即每次局部补偿量递减少,提高上机调试验证频次,这样能够有效提高模具整改效率。
冷冲高强板开发经验延伸
高强板零件开发难度比普板要大的多,重点在于型面回弹整改控制,既要考虑产品工艺性,又要考虑模具结构性,回弹多伦整改调试的方便性,还要考虑生产设备吨位的局限性。
高强板成形过程中容易产生塑性硬化,因此需要尽可能一次成型到位,应避免通过二次成型或是大整形工艺,否则容易造成整形开裂或是整形面不平质量缺陷。

高强板成形过程中通常需求的力量非常大,一些模具部件需要重点关注考虑反侧向力问题,否则很容易会造成冲裁产生毛刺或是薄弱镶块频繁损坏。
高强板零件质量状况多需要结合焊装总成综合来判断,当某一缺陷及其难以从根本上消除时,需考虑尝试对其环境件进行匹配优化,最终确保整个总成能够满足装车要求,而不仅仅只是一味地追求单件的质量状况,否则整改效果会适得其反。
高强钢板的模具型面研合率是决定产品型面回弹稳定的关键点,前后工序模面的符型研合尤其重要,现场验收检查该类模具时,需要认真识别一些着色假象。
高强板半工装出件后不要盲目去进行回弹整改,激光镭射边孔与模具修冲工艺有着较大的差别,因此需要尽快完成全工装模具进行联调改模,各工序综合分析才能制定出合理有效的整改方案。
高强钢板零件质量达到一定质量指标后,一些对设备参数、精度比较敏感的模具需要尽快进行母线调试匹配,如此会大大缩短整改周期和调试成本。高强钢板成形过程模拟的可靠性和准确性,仍然是CAE分析当前重点研究对象,全工序模拟(Fully cycle simulation)和回弹稳定性分析是必然的选择,当前的软件数值模拟大多数用于产品型面趋势变化判断,具体各数值造成的“假象”还需结合现场实际经验进行灵活的判断与识别,只有提高高强板工艺和回弹模拟的水平,才能切实提高单出制件精度。
采用仿真模拟过程中,材质各项参数以及各工序力量设定须与实际生产材料接近,可以提高仿真模拟的精准性。
制件整改调试过程中需要逐步做好板料毛坯尺寸,压机设备参数优化和固化,同时需做好调试验证记录,方便日后进行经验分析总结。