前言
随着汽车工业的不断深入发展,不仅在动力性、舒适性、燃油经济性等方面不断提升,造型及外观的精致感方面也不断提升,造型面的线条以及分缝R角及间隙都在做小,以提升精致感。这就对侧围、翼子板、车门等冲压零件的单品精度提出越来越高的要求。本文将从零件定位的角度,简单阐述对精度的影响,以及优先改善的方向。
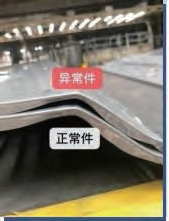
图1 某车型前门外板翻边长度的波动

图2 发盖外板轮廓的波动
生产现场常见的零件精度问题
在实际量产的生产过程中,门外板、发盖外板易出现翻边长度波动,导致总成包边问题。发盖外板易出现翻边轮廓线波动,导致整车匹配间隙变化,如翼子板-发盖的匹配间隙变化。翼子板、门外板易出现孔位变化,导致装配在上面的饰条发生错位,导致整车出现干涉,或者匹配间隙的变化,如门外板防擦条安装孔错位,导致防擦条安装后错位,进而影响整车间隙。
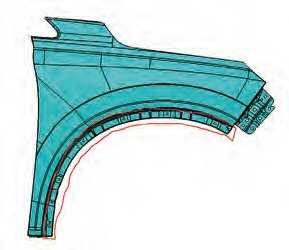
图3 翼子板轮毂孔的波动
精度波动的原因分析
零件本身深度较浅,又易产生回弹,靠型面的符型无法稳定定位。图4是某车型前门外板剖面图,整个零件很平缓,靠凸模型面本身零件错动量很大,无法定位。
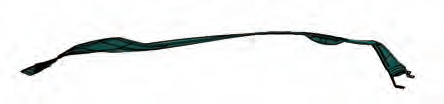
图4 某前门外板剖面图
零件在模具上是靠定位板定位的,定位的波动量一般都有0.5mm以上,定位的精准性不高。
图5所示的某车型前门外板OP40翻边工序,通过定位板限制零件边缘定位,本工序的工序内容主要是翻边。定位不稳定出现波动,主要导致翻边长度的变化以及门板下部防擦条孔位(这些孔在前工序已经冲出)的变化。
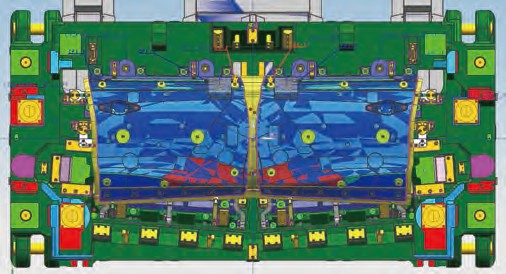
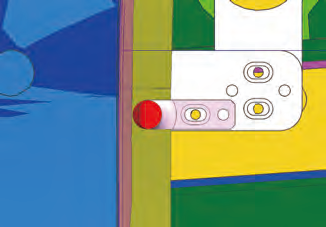
图5 某前门外板翻边工序定位
图6某车型发盖外板的翻边工艺,OP30主要完成大部分位置的正翻边及局部修边,OP40再完成最终的侧翻边。OP30、OP40未使用孔定位,而是用定位板定位轮廓,并不能使OP30、OP40的翻边轮廓准确传递,导致轮廓最终出现偏差。
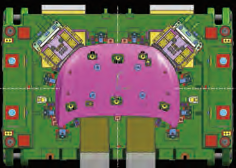
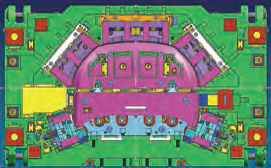
图6 某发盖外板的翻边工艺
精度稳定措施
使用孔定位
内板及侧围等零件,主要利用零件自身的孔来定位,无需在废料区设置新的定位孔。需要注意的是选取的定位孔一般就是制件的主副定位孔,在修边工序冲出最有利,孔大小φ16mm以上(对自动化有利),且孔方向与后序需求的冲压方向保持一致。图7是某车型后门内板OP30的定位孔。

图7 某后门内板定位孔
对于少孔或基本没有孔的外板件,孔定位的措施一般是在修边工序的废料区冲出定位孔,在最后的翻边工序使用修边/翻边复合工艺,实现翻边的同时切除定位孔废料。图8是某车型发盖外板OP40工序的定位孔。

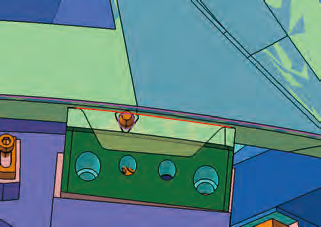
图8 某发盖外板的定位孔
合理的工艺方案
对于机械手抖动较大的老线体,使用孔定位在快速生产的情况下,零件定位孔的边缘,容易与定位销发生干涉,使边缘产生变形缺陷(图9),或者零件投放不到位,无法正常冲压。此种情形下,对于浅拉延靠型面符型很难定位的零件,建议尽量推进产品工艺改进,采用三工序的工艺排布方案,翻边在同一序完成(图10)。此方案不易产生轮廓波动问题,因翻边是在同一序完成,不会产生工序传递的变化。只需尽量合理布置翻边工序定位板的稳定性,将修边线的波动控制在0.5mm以内,对后工序的包边就基本不会产生影响。当外板件有锐棱的时候,使用精准的孔定位仍是最好的选择,否则外轮廓虽无异常,但棱线发生0.5mm的错位即难以接受。
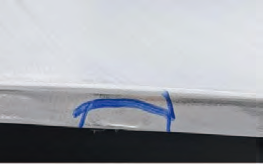
图9 某发盖翻边边缘变形
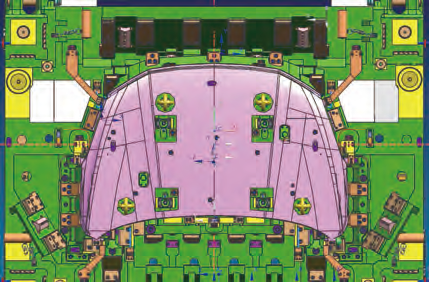
图10 某三工序发盖翻边工序
对于更复杂工艺的零件,无法少工序化且也无法保证全序都有条件使用孔定位,比如翼子板。这种情况的解决思路是所有翻边的轮廓线尽量在有孔定位的工序之前全部完成,保证整体轮廓稳定性。精度要求高的孔(比如饰件装配的定位孔)尽量跟随主副定位孔在同一序完成。
利用公差原则
绝大部分的安装孔和过孔,位置度公差都是采用最大实体原则。这意味着在公差范围内,孔径越大,位置度的公差带就越宽(图11)。比如图11,某安装孔的精度要求:孔径φ10+0.50,位置度±0.5,采用最大实体原则。当孔径是φ10时,位置度公差是±0.5;当孔径是φ10.5时,位置度公差是±0.75。孔径增加的0.5使公差带也加宽了0.5。所以对于此类孔,可以使用上偏差的冲头凹模,使孔径尽量走上偏差,这时对零件位置波动的容忍会适当加大。
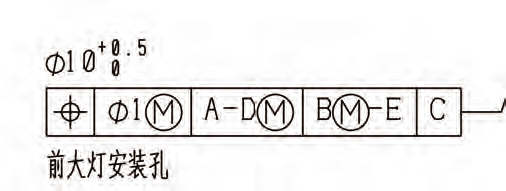
图11 某零件孔的公差要求
结束语
零件在模具上能够使用精准的孔定位,是定位稳定性的最大保障。但凡事都有局限,并非所有情形都能使用孔定位,此时应从工艺排布的角度,优先保证重要部位的精度,非重点位置有所舍弃,也可以适当利用公差原则,来降低位置波动的影响。未来智能制造技术进一步发展,可能有更加精准并且局限性更小的定位方式出现,更高精度地还原设计。