基金项目:镀锌板热成型技术研发与产业化(2211C004)
翟海峰 许杏泽 边文慧 王立然
精工汽车保定模具技术分公司,河北保定 071000
摘要 收集热成型模具开发现场问题,分析工艺设计CAE模拟分析与生产现场一致性的,从设计阶段进行问题预防,提高CAE分析与生产现场制件状态的一致性本文从制造现场热成型制件开裂起皱问题进行过程原因分析对策,总结现场经验,固化设计要求,实现开裂起皱问题的设计预防。
关键词 热成型;生产问题;开裂起皱;设计预防;
0 引言
冲压件热成型模具通过在成型镶块内部距离型面8-10mm的位置加工的均匀布置的冷却水道,对加热后的板材成型后进行快速冷却,实现淬火后的板材微观组织为均匀的马氏体组织,制造高强度性能的制件。因热成型镶块具有镶块材料成本高和水道加工后镶块型面可调整空间小特性,因此在设计阶段充分识别制造风险,生产过程减少整改,是控制模具开发成本的关键。本文基于热成型模具开发过程实际生产问题,对设计阶段工艺和结构设计进行优化。
1 镀锌板锌层脱落引起制件开裂问题
1.1问题描述:镀锌板制件成型过程中,几字型之间端头深拉伸位置制件开裂。
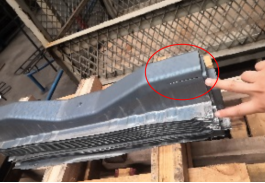
图 1制件开裂
1.2原因分析:①制件成型性CAE分析满足最大减薄和线性失效参数要求,板料成型性能无问题。②现场观察拉延筋凹槽位置有积灰,经分析拉延筋设计为凹筋,生产中板料流动,脱落的粉屑沉积在凹筋中,造成板料滑动阻力加大,成型过程制件开裂。
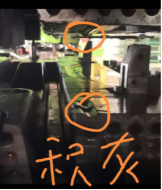
图 2现场制件积灰

图 3拉延凹筋位置
1.3现场对策
采取以下措施:在下模拉延筋积灰位置增加吹气装置,消除积灰对成型的影响,整改后制件开裂问题消除。
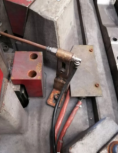
图 4整改效果
1.4设计预防
①工艺设计阶段压边圈位置采用如图方式设计,且分模线设置于R角边缘,使生产中脱落粉屑从分模线位置掉落②结构设计阶段在积灰位置增加吹气装置
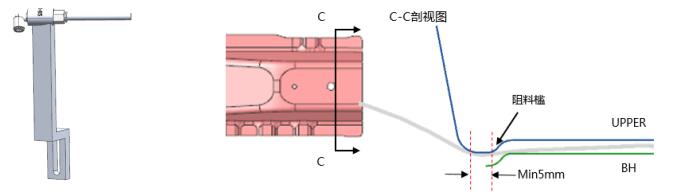
图 5设计预防
2.行程设置对制件成型性的影响
2.1问题描述: A柱加强板下段调试过程中制件法兰起皱,影响制件品质。
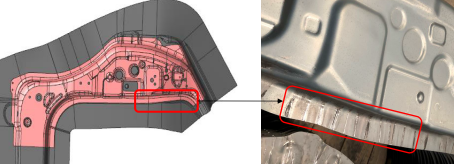
图 6制件起皱
2.2原因分析
2.2.1产品造型:产品两侧棱线趋势差别大,棱线1为外凸造型,成型过程材料流动按蓝色虚线方向,棱线2为直线型,成型过程材料按红色虚线方向流动,成型过程都为收缩变形,存在成型过程板料起皱风险。
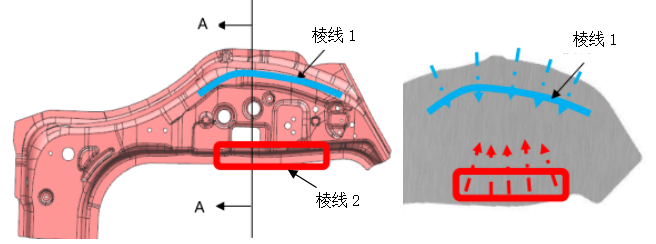
图 7材料流动方向
2.2.2成型过程分析
1)成型方案设计:基于制件两侧拉伸深度不同,分别设置binder1和binder2;
①成型过程Binder2先闭合,料片接触棱线1处并向下成型后,Binder1再闭合。
②由于棱线1为外凸造型,棱线外侧材料按蓝色收缩成型,binder1未闭合前,棱线2处材料为自由状态,按红色虚线流动集聚,导致起皱。

图 8成型过程
2.3整改对策
抬高内侧Binder1行程(45mm改到75mm)(在上模接触板料变形集聚之前,使两侧压边圈都闭合,改善起皱)
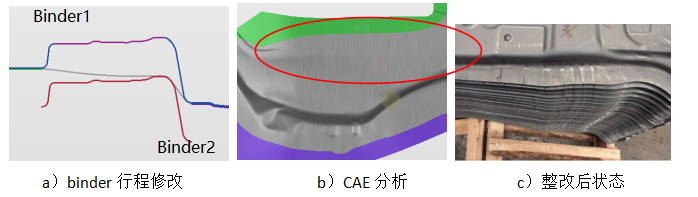
图 9整改方案实施
2.4设计预防
制件成型过程两侧分别设置binder,且制件存在外凸造型的需满足以下两个条件:①优选两侧压边圈同时闭合,无法同时闭合时,要在较深侧成型引起材料流动变形之前保证较浅侧压边圈(binder1)先闭合。②CAE 分析-过程无明显起皱。
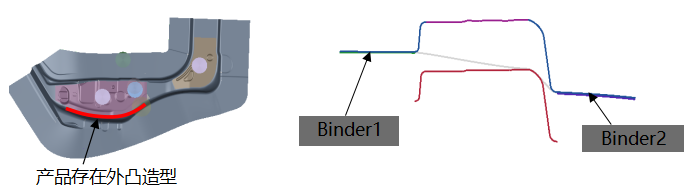
图 10设计预防
3.总结
热成型模具是在传统冷冲压的基础上创新的新的成型方法,生产过程产生新的变量因素如板料加热成型性能变化,成型过程局部锌层脱落等生产经验需要不断积累,在设计阶段通过成型工艺方案的充分验证和模具结构的创新对生产问题进行设计阶段预防。
创新点说明:拉延筋成型位置增加吹气装置,解决锌层脱落积灰成型阻力增加对制件成型性能的影响。