3D打印是一种金属加工技术。特别是金属3D打印提供无与伦比的设计自由度,且具备广泛材料制造的应用范围;但是,此技术仍然面临生产效率低下、质量不稳定以及最终成品机械性质的不确定性。对于使用3D打印制程的公司,目前所面临最大的障碍,就是在3D打印时所产生的变形。目前部分领先的企业研究的3D打印热应力仿真软件,最大功能为可预测构件在3D打印、热处理及支撑架移除时,整体最大应力与变形。相关功能包含计算最终构件的变形,减少/避免变形、最小残留应力、优化积层方向、底板和支撑结构的移除制程,目的可协助客户第一时间决定正确的3D打印方案。
现有激光3D打印过程由于粉体、气场与激光作用下,可能造成腔体透镜的污染,激光长期使用下可能衰减其出光能力,或腔内粉尘影响其激光行进路线,这些都可能造成激光单位能量之改变;激光3D打印若在逐层制作无实时侦测与预警,内部瑕疵将残留在内结构里甚至制程会因此中断,因此架构闭回路3D打印系统将需整合监控装置,进而整合侦测瑕疵侦测等,达到工作中确认与逐层确认的完整机台状态监控之目的,提高系统制程与设备稳定及强健性。
3D打印技术依据美国材料试验学会(ASTM)订定之标准,共可分为七大类型。分别为光聚合固化技术(Vat Photopoly merization)、材料喷涂成型技术(Material Jetting)、黏着剂喷涂成型技术(BinderJetting)、材料挤制成型技术(Material Extrusion)、粉床熔融成型技术(Powder Bed Fusion)、
迭层制造成型技术(Sheet Lamination)与直接能量沉积技术(Directed Energy Deposition)。依不同之成形制程技术,有其适用之材料。
因金属产品组件的强度及结构特性具有其设计要求,金属3D打印制程与其他材料相比,制程困难度更高。此外,金属3D打印属于高温成型技术,在应力应变方面之控制处理更为重要。非优化之制程参数或不稳定之制程参数将会造成产品产生缺陷,如制程迭层分离或裂缝缺陷(如图1所示)、悬空结构(overhang)外型异常(如图2所示)等,甚至产生内部之微结构缺陷。这些问题对于应用导入均造成产品寿命及强健性之隐忧。

图1 制程迭层分离或裂缝缺陷
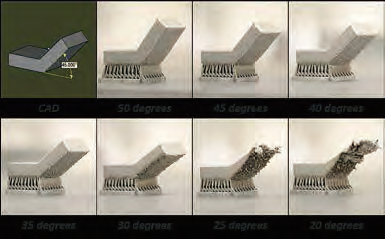
图2 悬空结构(overhang) 外型异常
传统的3D打印流程(如图3所示)说明如下:①设计图档载入;②根据经验进行制程前处理,其中包含制程参数设定、扫描策略与摆放姿态决定以及支撑结构设计与补强等等;③进入实际制作,最终将透过逆向扫描进行成品尺寸相关品保控制。
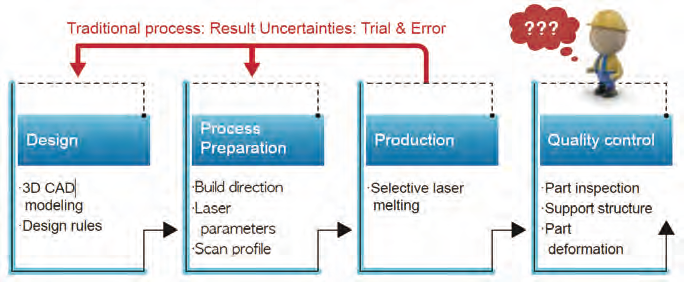
图3 传统3D 打印设计制作流程金
但在3D打印导入前期,此流程往往因缺乏经验导致开发不同材料制程相当困难,以致制程缺乏稳定性。一般需透过实验试误法需花费三至四个月时间进行制程参数分析,试误过程耗费成本且效率低。
总结以上几点,建立金属3D打印材料、制程、制程系统、质量之规范标准,将是目前亟待进行之工作。工研院激光中心近几年致力于建置3D打印技术之智能化系统,目标完成制程仿真软件开发、设备监控补偿系统以及远程多信息分析诊断系统,实践3D打印之虚实整合智能制造。相关技术可于制作前提供较佳制程参数与可行性分析,缩短材料参数开发时间,减少制程热残留应力影响之失败可能。此外,开发之监控补偿系统目标实时监视粉床及激光质量,针对制程缺陷或变化实时分析并提供补偿控制参数与对策,所建立之智能制造系统包括制程相关信息收集与分析诊断,远程可实时预警并提供完整制程履历,未来可衔接整厂复合系统智能化制造目标。
金属3D打印预前热应力模拟技术
金属3D打印的选择性雷射熔融(Selective Laser Melting,SLM)技术与传统焊接物理相当类似,SLM可想象为数以万计的微焊接成型技术,而SLM的热应力物理特性与焊接问题相当
接近,但量级相差甚大。借于相近的物理特性,工研院激光中心以焊接物理的固有应变法(Inherent Strain Method,ISM)为基础,开发一金属3D打印专用之预前热应力软件(ITRIA MSim),与传统透复杂热-机械偶和模型差异,ITRIA MSim结合实验优化技术与弹塑性力学理论,可快速地完成制程热应力与翘曲变形的预前分析,快速回馈进行制程参数修正优化,降低试误法的成本。以下将以金属3D打印火箭引擎燃料混合喷射器做为案例说明。
晋升太空与工研院激光中心合作开发火箭引擎燃料混合喷射器,如图4所示,从初始设计进化发展到适合3D打印制作的设计修改(DesignforAM,DfAM)来回多次,最终由激光中心负责进行制作。此燃料混合喷射器大小为110mmx110mmx170mm,制作时间单一件约需4天时间,但此工件因属大尺寸工件且结构复杂,导致制程设计相当困难。主要原因是大工件在制程中累积的热应力会较大,更容易造成支撑断裂工件翘曲导致铺粉刮刀被干扰甚至停机。若制程在前段时间就发生停机,在未完成的情况下不太容易看出接下来的制程会有无其他风险,这也是大工件透过实际制程进行试误法所面临的问题:失败次数通常大于2次以上,这无疑浪费了许多额外时间与金钱,而虚拟制造正是为了降低制程风险、减少制造成本而开发。

图4 3D 打印燃料混合喷嘴几何设计( 左);晋升太空研发之火箭引擎( 右)
透过预前模拟可以得到如图5之变形预测结果,可发现在预测结果中变形量超过0.5mm的深红色区块皆为制程中会发生问题的区域,而这结果也符合实际制作结果,特别是成品中支撑断裂与工件变形的高风险区域。预前制造可预测出制程高风险区域,在制程开始前预先提供高制程风险发生位置信息,让制造者加强该些位置的支撑结构,以提高制程良率。以此案为例,预前模拟时间只需40分钟,与实际制程4天相比快上许多。除速度上具备优势与成本大幅节省外,预前制造还可完整提供工件内部无法轻易观察位置的风险,协助使用者改善设计提高制程良率以满足精准制造之需求。
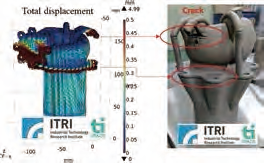
图5 虚拟制造结果可预测制程中风险较高区域
工研院激光中心将预前仿真技术开发成一软件ITRIAMSIM,如图6所示,透过用户友善的接口,希望不具备仿真背景的使用者也能轻易操作使用并得到制程设计改善信息。此软件加载STL图文件,内建五组材料数据库(钛合金Ti6Al-4V,钴铬钼合金MP1,不锈钢PH1、316L以及铝合金AlSi10Mg),数据库中材料是经过ITRIAM机台校正之数据,用户只需经过一次实验校正即可对不同设备进行预前模拟。开发此软件开的目标为加速制造者经验学习曲线,降低制造成本于提高制造效率,协助产业升级与创造更多高值化产品。

图6 工研院开发之ITRI AMSIM 软件
熔池监视补偿控制技术
现有激光3D打印过程在+粉体、气场与激光作用下,可能造成腔体透镜之脏污,因此激光长期使用下可能衰减其出光能力,或腔内粉尘影响其激光行进路线,这些都可能造成激光单位能量之改变。若激光3D打印在逐层制作无法实时侦测与预警,瑕疵将残留在内部结构里,甚至制程会因此中断。因此架构闭回路3D打印系统将需整合熔池监控装置,进而整合侦测熔池影像、形貌轮廓甚至熔池温度等,达到工作中确认与逐层确认的完整机台状态监控之目的,达到预警及制程回授追踪再确认,如图7所示。
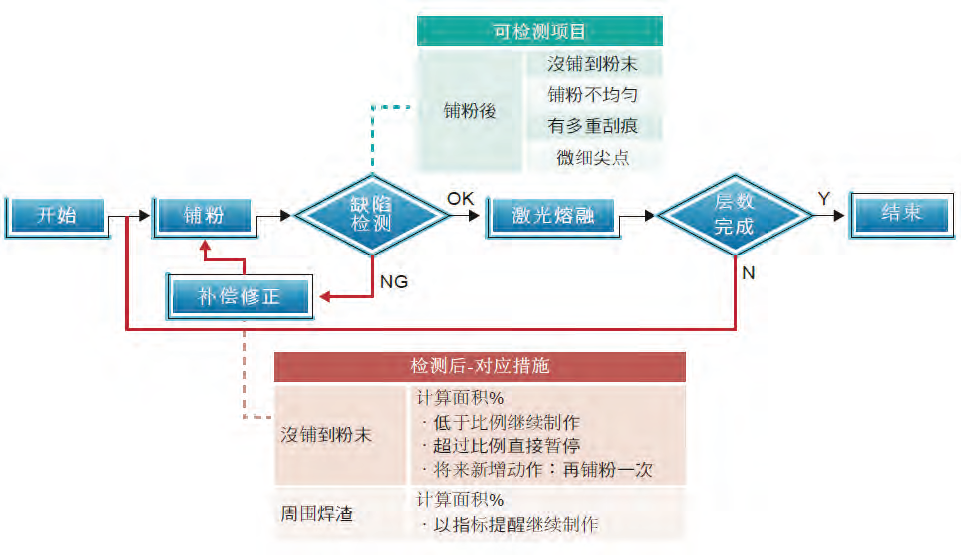
图7 侦测铺粉完整度与对应措施
工研院激光中心在去年度已达到制程良率改善≥80%的目标,导入侦测铺粉完整度达>90%以上监控判断成功率。若侦测有铺粉不均匀、缺粉未覆盖区、刮刀磨耗过大造成铺粉不均匀痕迹,将自动判别后再进行重复补粉铺粉动作,于警戒上限到达前以不中断制程为优先条件,使未覆盖区域得到再铺粉以及实现人员通知调整的机制,实现制程缺陷补偿控制。另外功能包含设备的氧量浓度、循环流速、腔体压差、底板温度达全时100%条件追踪监控。当因氧气浓度变异回升、循环流速因循环熔渣逐渐阻塞而变慢,都会实时调整循环频率提高效率直至目标值达到正常区间。透过以上两点的缺陷影像与条件变异所进行的补偿控制,目标于导入此系统后可让产品良率提升>80%。
多参数补偿虚实整
目前激光中心的多参数补偿虚实整合已完成远程激光3D打印实时诊断设备制程监控,并可侦测氧气浓度、压差与腔体流,若有发生门坎超过会提供预警功能(如图8)。讯号更新频率为1sample/sec,预警综合判断于3sec内完成。目前已完成三台设备进行连网,如图9所示,连网后远程预警诊断可
<5sec。虚实整合平台采用Modbus
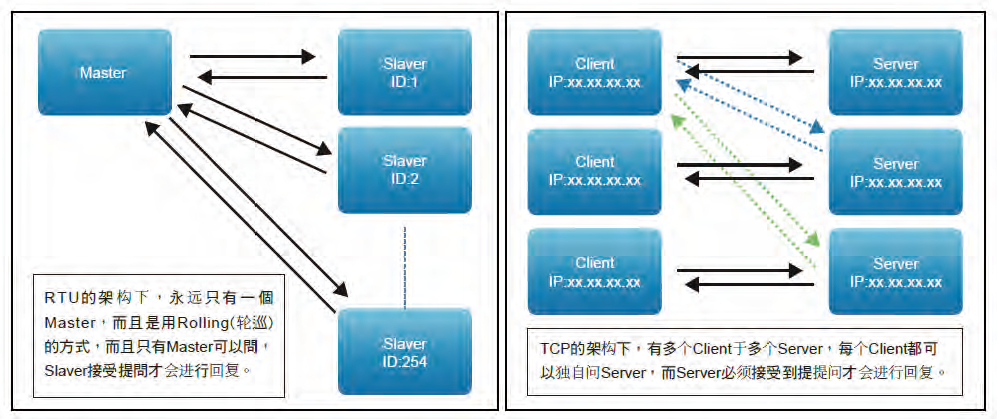
图8 Modbus TCP/RTU
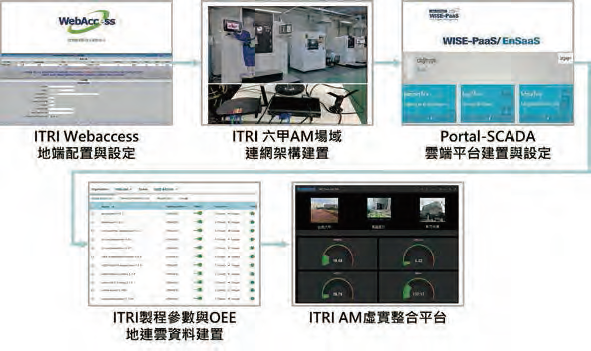
图9 金属3D 打印数字转型平台建置流程
TCP/RTU方式让Webaccess跟设备通讯,Webaccess是Master;设备都是Slaver。利用MQTT协议(如图10所示)传输实时数据,并且透过GafanaDashboard监视、预警通知软件提供画面供用户获取信息。
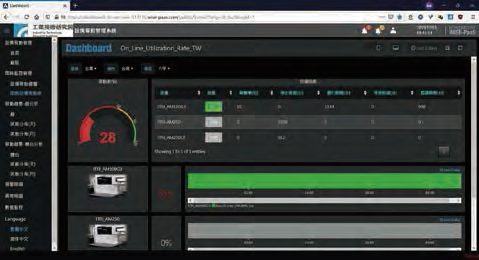
图10 ITRI 多参数虚实整合云平台( 计算机)
预前仿真技术结合数字监测 大幅提升加工质量及效率
工研院激光中心针对金属3D打印开发预前热应力仿真技术,透过物理模型进行SLM制程前模拟,达到制程风险预警之效果,可有效协助制造者强化设计以提高制造成功率。预前模拟目的为制程可视化确认高风险区域,在火箭引擎燃料混合喷射器案例中,每一实际制程需耗时4天且结果含不确定的失败
因素,透过约40分钟的预前模拟,可完整掌握高风险区域信息,并协助相关设计强化以提高制程良率。此技术已开发成一套软件ITRIAMSIM,期望透过预前模拟技术协助制造者加速新产品之设计制造,提高金属3D打印设备投资报酬率并加速产业升级。
另外,工研院激光中心亦建置3D打印制程良率透过铺粉侦测与条件监诊SaaS与PaaS云端平台,从制造管理经营者与研发单位需投入生产数据的筛选与分析,转化出3D打印过程的制程数据与生产数据,制程数据将可作为回馈每批次零件生产质量与参数回归分析,生产数据将能转化嫁动率与生产性能,进而转成金属零件供应链的时程与效能估算。借由积层制造参数仿真、瑕疵检测与预警,持续验证3D打印所完成制品的最终质量,结合数字平台的制程生产数据,便可逐步透过数字平台完善生产流程。