从1998年起,欧盟开始提倡减少碳排放,当时仅限于口头协定,没有强制约束;2014年欧盟正式设立全球最严格的汽车碳排放控制目标,以法律形式强制要求汽车企业减少碳排放,目标要求2021年汽车厂将汽车降低二氧化碳排放量27%,2021年必须覆盖所有在欧盟范围销售的新车,汽车企业无法达到上述标准,超出碳排放标准的车辆将受到欧盟每辆车95欧元/g罚款,这项汽车碳排放控制适用于所有欧盟28个会员国境内销售的汽车,为避免遭受罚款,主要汽车企业纷纷采取因应措施,最简单的方法是生产电动车辆。

图1 是主要汽车生产国家碳排放标准。
降低碳排放(汽车燃油消耗)是全球主要车厂最重要的研发课题,达成手段之一是藉由传统汽车零部件转为电动化、电装品轻量化、引擎小型化,提升运转效率。例如为节约能源,设计整合式启动马达与发电机,在停车时配合自动启闭系统(Start/Stop)作动,藉由高电压零部件设计,使搭配的零部件如IC半导体因此承受较低电流,降低系统成本,周边附属零部件得以简单化,整合式启动马达与发电机可于怠速(Idle)与煞车时做能量回收动作,有效减少能源消耗。
因应节能减碳潮流,新能源车辆与电动车辆是未来车辆发展焦点,无论是新能源车辆或电动车辆,车身中皆须应用大量的电力电子组件,各项零部件对电力的要求更胜以往,即使传统以机械为主的零部件,目前已发展到透过电子组件控制以求高效、精准目的,在这样的趋势发展下,动力系统电动化程度日益提升,部分零部件因应车辆电动化,须重新设计/开发以期符合需求,而对应车辆系统用电量增加,应用高效节能电力组件亦为车辆电动化发展重点。
电动车辆藉由电动化零部件改善污染排放,以电动控制或电力电子零部件创新设计,改进运转效率与延长行驶距离,汽车依动力电池配比多寡电动化程度区分为纯电动、全混、轻混与微混动力系统,简单地说就是电池电力与电动马达担负动力系统的配比差异性,纯电动车表示完全使用动力电池作为电动化动力。
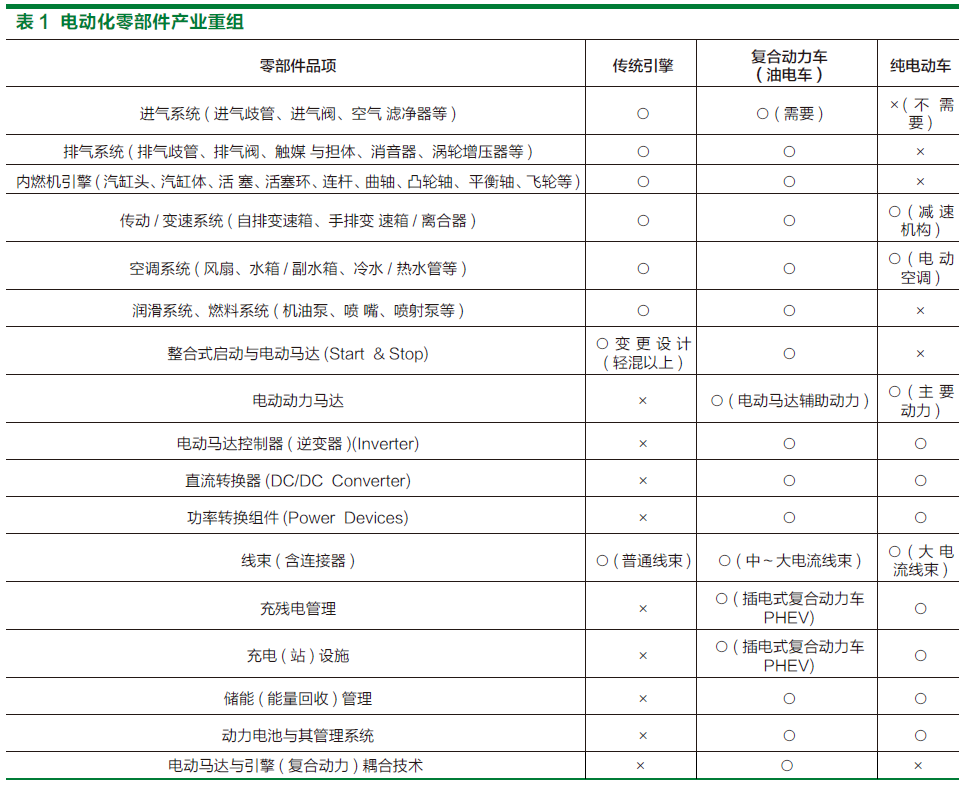
汽车产业重组与零部件产业转型
电动车辆利用电动马达、动力电池取代原有(汽油或柴油)引擎、燃料系统,作为电动车辆主要动力来源,属于传统内燃机引擎的进/排气系统或燃料供应系统、变速箱、油压装置、倍力装置、总泵、转向系统等零部件,亦变得精简或不再需要,改由电子零部件控制电动车的启动、运转、停止以及加减速等。
除此之外电动车还在传统汽车既有的悬吊系统、车体、轮胎等装置上面,增加避震弹簧、避震器、悬吊臂、电动空调系统、高压线组等零部件随着车辆系统朝向电动化、电子化趋势发展,动力电池、电动马达等电子零部件占整车成本的比例明显增加,原有的引擎、变速箱等燃料系统在整车成本的比例逐步减少,传统车辆与电动车辆零部件种类与选用差异,如表1所示。
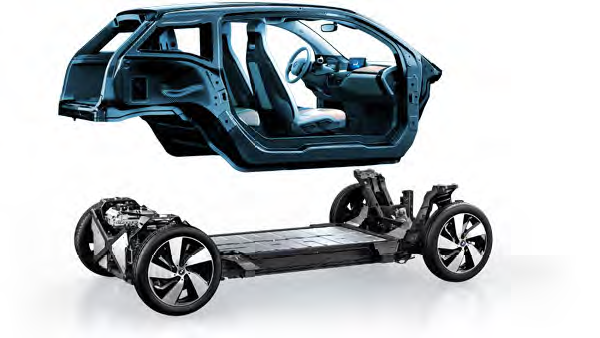
图2 BMWi3 座舱(Cabin) 使用CFRP 复合材料实例
动力电池在电动车辆成本所占
的比重最高(40%~50%),其次是驱动系统,成本占比由原先传统内燃机引擎的22%~24%,降低到10%~20%。其中电动车辆利用电动马达(33%~43%)、电动马达驱控器(39%~47%)、汽车整车控制器(4%~8%)、传动机构与传动轴(8%~10%)、冷却系统(4%~6%)取代既有的引擎(35%~40%)、辅助设备(18%~22%)、传动机构(20%~27%),以及排气系统(8%~11%)。电动车辆其他成本则包含车壳(8%~19%)、底盘(5%~9%)以及其他零部件(6%~15%)等。因为电动车辆衍生许多传统(内燃机)车辆新增加的控制器、动力电池、功率组件或功率转换模块,形成整车与零部件产业重组现象,也为电动车辆整车与零部件开启产业转型机会。
汽车轻量化与模块化零部件
汽车轻量化可透过生产小型车辆、改善汽车结构与使用轻质合金、高强度钢板或橡胶与塑料材料等方式达成,车辆可以小型化系因汽车采用了前置引擎、前轮传动,取消了传动轴、差速器齿轮等零件,使结构更精简,其它结构上的改善如使用高强度钢板、中空结构及小型化等,在欧、美、日车厂已逐渐落实,橡胶与塑料材料于汽车使用量快速成长,因应汽车轻量化的做法受到相当重视,竞相提升轻量化材料在汽车上的使用比例,其中橡胶与塑料材料无论是重量、制造性、材料成本等,都具汽车零部件轻量化材料使用优势,使用量逐年增加。
车厂透过生产小型车辆、精简汽车外型设计、零部件小型化设计与使用轻质合金等方式达成汽车轻量化的目的,近年来汽车为兼顾乘坐空间与传动效率,采用前置引擎与前轮传动,取消后传动轴、后轴差速器与齿轮组等零件,使结构更精简;其它如车身板金材料、制造方法与机构改善、中空结构设计及小型化零件应用等,在欧、美、日的汽车业者逐渐落实,各车厂竞相提高轻质合金在汽车零部件的应用比例,其中又以高强度钢板、铝合金、镁合金、钛合金等轻质合金最受瞩目。
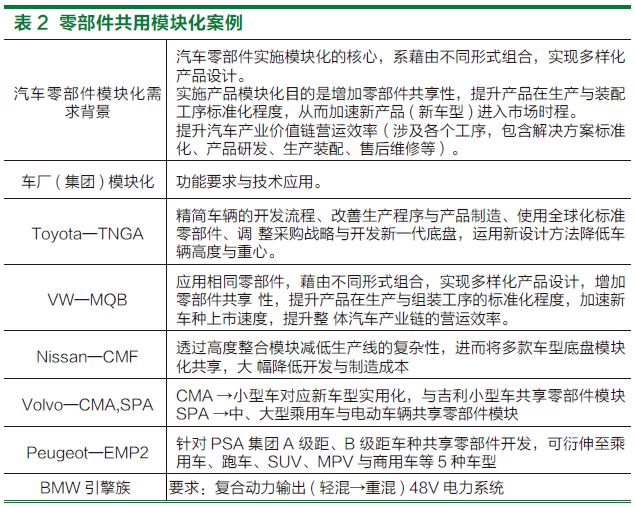
轻量化汽车零部件实施方法
实现电动车辆轻量化主要有几种途径:一是采用轻质材料,如使用低密度的铝及铝合金、镁铝合金、工程塑料或碳纤维复合材料等,使用高强度钢板替代普通钢材,降低钢板厚度,二是优化轻量化结构设计,对汽车车身、底盘、引擎等零部件进行结构优化,三是采用先进的制造技术,如雷射拼焊、液压成型、铝合金低压铸造与半固态成型技术。
电动车系由车体、底盘、动力机构、悬吊、轮胎、电池组、转向机构、剎车机构、电动马达与空调等系统零部件或模块所整合而成,其中车体与底盘占电动车总重约2/3比例,电动车轻量化的重点在于车体与底盘零部件设计与制造,车体与底盘轻量化有助于电动车整车减轻重量。电动车轻量化可藉由车体结构设计(优化设计、减少零部件数量、创新结构设计)、轻质材料应用(橡胶/树胶、轻质合金或高强度钢板、碳纤维等复合材料等)、制造技术(成型技术、零部件链接组装技术或异质接合技术)等方式达成轻量化目的。
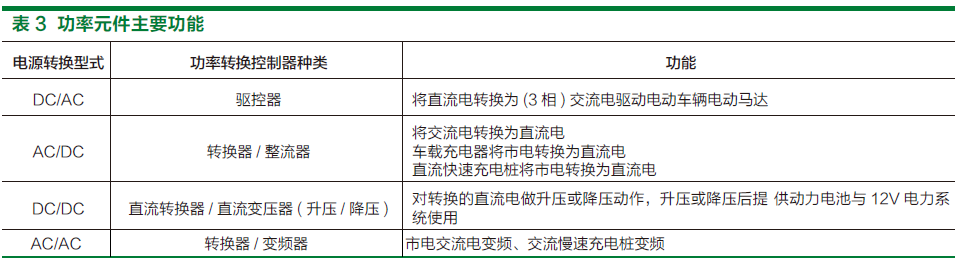
电动车轻量化主要关注在两个方面,其一是基于改善电动车电力消耗的轻量化,其二是基于提升电动车性能与安全性能的轻量化,电动车轻量化可藉由下列方式达成,如(1)车辆小型化,
(2)车辆重新设计与零部件减量,(3)轻质材料选用,具体实施方法可分为零部件设计与制造。
越来越多的电动车辆零部件采用碳纤维复合材料,由于质量轻巧与机械强度等特性,全球主要车厂竞相开发与试量产,目前碳纤维复合材料被开发应用于汽车零部件的实例计有车身、底盘、车顶、车门、汽缸头盖、引擎盖、尾翼、压尾翼、中控台、装饰条、仪表盘、传动轴、特殊动力传动系统、座椅、座椅垫、尾翼扰流板、后视镜外壳、车架悬臂、车侧裙摆、导流罩、A柱、遮阳板、散热器护罩、侧护板、踏板、副保险杆等车身、内饰件与外饰件等,如图2是BMWi3座舱(Cabin)使用CFRP复合材料实例。
汽车零部件产业已经跨越国界演变成跨国企业并在全球竞争,且竞争越来越激烈,世界各国的消费者对汽车零部件的要求呈现多样化,零部件发展趋势是要求在各方面的性能不断提升,例如安全性、可靠性、污染物排放、油耗/碳排放、设计实用性等,而汽车产业经过100多年的发展,创新性产品开发难度不断增加,诸如上述因素导引车厂在汽车零部件研发投入巨大心力,车厂还必须承受零部件制造、管理、市场推广、售后、库存等巨大的成本压力,汽车零部件模块化提供了精简化与降低成本的对策。
零部件模块化的概念逐渐被车厂开发应用,以VW汽车为例,从产品平台化衍生出来的零部件模块化开发,是对应激烈的市场竞争的必要手段,VW提出模块化战略,实施MQB平台产品开发计划,汽车零部件模块化开发必将成为未来汽车产业研发与制造的趋势。另外,以Tesla为代表的电动车整合技术则显现汽车产业未来的发展,电动车的结构由于省略传统引擎、变速箱、传动轴等复杂的机械零部件或系统,所以整车设计更容易导入模块化理念,未来汽车设计将与目前ICT产品一样,具备高度标准化与共享化特性,组成最终产品的各个次系统(Sub-System),都将由模块化的开发方式因应。
主要车厂汽车零部件的模块化已达到车门模块化、仪表板、内饰件、车身等模块化,如VW的MQB、Nissan的CMF、Toyota的TNGA等,表2所示,是汽车集团整合资源,零部件共享与模块化案例。
Hyundai将使用Canoo的EV滑板式底盘应用于各式电动车辆,与电动新创公司Canoo合作,共同开发紧凑型与超小型电动车架构,预计在2025年之前推出11款电动车,希望使用Canoo的滑板式底盘新平台,简化电动车的开发流程与降低成本。
功率转换控制器是电动车辆产业普及化决胜点
电动车辆整合汽车电子应用导致汽车电子产值逐年增加,半导体功率组件简称功率组件,是电动车辆电子装置的电能转换与电路控制核心,主要用途包括变频、整流、变压、讯号处理与控制等,同时具有节能功效,功率组件逐渐应用于电动车辆等领域,功率组件须具备功能有:(1)在各种应用中具备更高能源效率;(2)更高的载流能力,在600~1200V典型电压条件下,载流能力需达100~300A;(3)更优异机械与电气性能,确保能够承受恶劣汽车环境,同时满足防失效设计所有安全与保护要求;(4)更低的电磁干扰与寄生电感,由于大电流切换或转换与高电压会产生极强的电磁场,包括传导或噪音/电磁干扰与对汽车感应电子装置造成影响等。
由于轻混复合动力车的电动马达功率有限(不足20kW),所需的电池电压比全复合动力车或纯电动车的电池电压低,为降低各种功率组件成本(电池、控制器、切换开关、电容器等)考虑。现阶段轻混复合动力车使用200V电压,而全复合动力车或纯电动车电压则高达450~1500V(在安装升压器的条件下甚至更高),所有的复合动力车辆均使用驱控器(Inverter)做为电动马达驱控器,并多导入绝缘闸双极晶体管(IGBT)或金属氧化物半导体场效晶体管(MOSFET)应用,由于功率输出特性,IGBT已被视为最佳性价比的半导体开关组件。为达到最优性能与最低损耗,需要优化驱控器转换电压(降低系统的整体杂散电感),并缩小电压与IGBT阻断电压的差距。
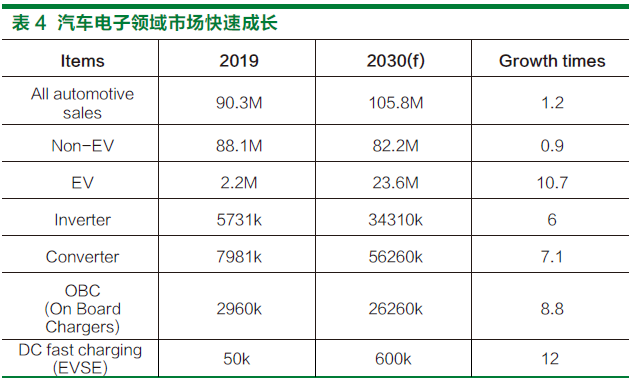
尽管传统引擎汽车可以相对轻松地从12V电池供电与相对应的12V/14V交流发电机获取车载系统电气需求。由于复合动力车采用几个系统,需要更高的功率等级,对轻混复合动力车、全复合动力车、插电式复合动力车或纯电动车而言,耗能最多的当属电动马达驱动装置,该装置需要在没有引擎支持情况下,至少在一定时间内能有效驱动车辆行进,半导体功率组件在电动车辆(复合动力车、纯电动车等)扮演重要角色,表3,是功率组件的主要功能。
电动车辆的高压电力应用,导引电动车辆采用两种功率模块,将直流转换为交流型态,以便驱动电动马达的DC-AC驱控器,以及在高压电力与12V电力之间实现电能交换的直流转换器,复合动力车仍需要12V电力,因为多数标准汽车电子系统都采用12V电力(如车内灯照明、方向灯等),驱控器与转换器处理或转换几千瓦(kW)的功率输出,需要配备优化半导体功率组件与复杂的高效能电子装置。
功率组件主要应用在电动车辆功率转换控制器,包含驱控器、直流转换器、车载充电器与直流快速充电桩等,随着电动车辆比例增加,从2019年到2030年,全球HV/PHV/EV/FCV系统明显成长,销售量将迅速增加,2030年全球电动车辆系统产值预估1969亿美元,较2019年成长约6.2倍,如图4所示。预估2030年全球电动车市场2360万辆,较2019年成长10.7倍,与电动车相关功率转换控制器成长6~12倍,功率转换控制器将是电动车辆系统需求成长快速且关键的产品。
线传控制零部件的创新应用
线传控制(X-by-Wire)系统源自飞机驾控(Fly-by-Wire)概念,已于航空与军事车辆行之有年,使其应用载具得以表现优异操控特性并提高系统可靠度,线传控制系统将成为先进车辆与汽车的技术发展重心,因应汽车导入市场,多数与车辆安全相关之机械操作次系统(Sub-system),逐渐更换成具高可靠度的线传控制,其中X代表与汽车安全相关的操作,线传控制是藉由车载控制网络(CANBUS)通信协议链接电子设备,藉以控制引擎或机构的方式,其控制系统都可藉由机械或油压装置,将传统车辆上原先各自独立操作的复杂机构或零部件改以讯号取代或整合,并经由车辆行车计算机控制,大幅提升电动车辆操纵性与安全性,汽车机械结构得以因此精简化,进而提升车辆设计灵活性,达成轻量化的目的,汽车电子应用技术的突飞猛进,线传控制将成为新一代汽车设计的重要议题。
目前已上市的传统汽车或汽车多有线传控制的应用例子,线传控制计有线传转向控制、线传悬吊控制、线传煞车控制、线传油门控制、线传排档控制等应用方式。
汽车导入线传控制应用,可以省略传统的气动、液压或机构,取而代之的是传感器、汽车电子控制单元、电磁的执行机构,传感器精度、控制单元硬件可靠性、抗电磁干扰性、控制算法的可靠性与容错性、执行机构的快速性、各系统控制单元之间的通信实时性、车载控制网络整合能力等,攸关线传控制的功能与应用。

图3 Nissan Murano 线传转向控制应用实例
线传转向应用实例
汽车转向系统的基本性能是保证车辆在任何情况下转动方向盘时有较理想的操纵稳定性,随着汽车电子技术的精进发展与汽车功能系统的整合,汽车转向系统从传统的液压助力转向系统、电控液压动力转向系统,发展到现在逐渐推广应用的电动液压动力转向系统。
典型的线传转向系统由方向盘总成、电控单元与转向执行机构等3大系统所组成,负责感测驾驶员驾驶意图的转角传感器与转矩传感器,整合在方向盘总成系统,为了提高系统的可靠性,电控单元通常设置3组及以上,各系统互为安全备份,当某一系统电控单元发生故障时,备份的电控单元立即接手,防止故障发生,线传转向系统与现有的电动动力转向(EPS)比较,最大差异是省略转向机柱等机械结构。
精简转向机柱后,线传转向系统的结构配置可以大幅简化,原有的刚性连接机械零部件逐渐被电子讯号线所取代,不仅节省驾驶舱空间,还可以删减转向系统与机构的重量,提高汽车燃油经济性。此外由于传统的刚性连接机构被取代,驾驶不再承受到路面颠簸所带来的方向盘振动,汽车发生正面碰撞事故时,驾驶员不至于受到转向机柱的撞击伤害,节省出来的空间可以配置腿部安全气囊,从而改善汽车安全性。
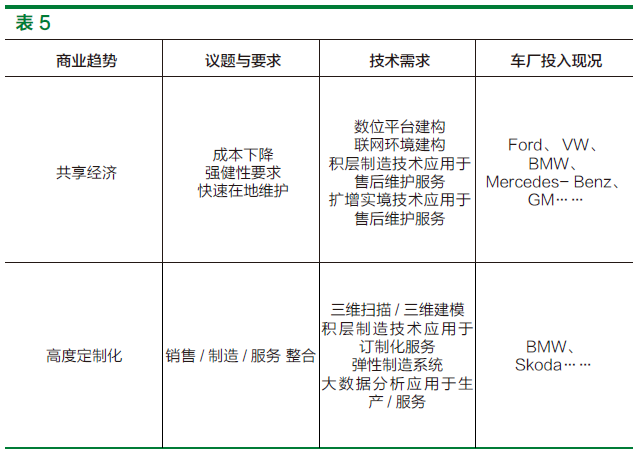
NissanMurano线传转向的理念是源自EA2的概念车设计,图3是NissanMurano线传转向控制应用实例,透过线传转向技术的应用,可大幅简化转向机构零部件,精简车辆配置空间,新一代的汽车设计因此变得更具弹性,透过线传转向的优化设计技术,可精简机构件数量与配置空间。
导入智能制造零部件产业精进
汽车已进入产品多样化及生命周期缩短的时代,以汽车产业制造业为例,2000年各主要汽车厂能够提供的车款并不多,如BMW当时只有12款车型可供选择,2017年增加到28款,车型选择款式增加后,反而导致车型生命周期缩短,BMW新车款生命周期从以往131个月缩短到106个月,如何依照消费者需求调整产能,成为汽车厂与汽车零部件企业必须严肃面对的课题,适度对应汽车零部件生产效率、研发与制造成本、不良率、高值化,甚至是零部件物流调度等。
未来的汽车产业将朝共享经济与高度定制化的趋势发展,因应共享经济汽车产业需求,汽车产业将要求成本下降、强健性要求、快速在地维护,可能支持的制造技术计有数字平台建构、联网环境建构、积层制造技术应用于售后维护服务、扩增实境技术应用于售后维护服务。
因应高度定制化汽车产业需求,汽车产业将要求销售/制造/服务的整合,可能支持的制造技术计有三维扫描/三维建模(3DScanning、3DModeling)、积层制造技术应用于定制化服务、弹性制造系统、大数据分析应用于生产/服务等。
因应共享经济新商业模式兴起,汽车产业制造技术需求将会有所变化,新的共享经济模式将会造成汽车所有权及使用模式变化,汽车所有权集中于营运者,汽车使用率大幅增加,相对地,汽车零部件耗损率提高,对于汽车强健性以及实时维护需求提升。拥有汽车个人使用权模式仍会存在,但会转向定制化趋势,以彰显个人设计风格及品味,因此订制化服务及弹性制造方式将应运而生,导入智能制造具有下列意涵:
(1)引进自动化设备,增加产量;
(2)降低生产与材料成本,提升附加价值;
(3)提升专业人力素质,解决缺工的问题;
(4)改善汽车零部件供应体系效率,改善服务质量;
(5)链接产销信息,提升工厂管理效率;
(6)配合智动化生产,缩短设计与研发时程,快速进入市场;
(7)强化定制化与少量多样产业需求;
(8)创造新一波的就业机会;
(9)促进异业结合,创造价值。
新世代车用零部件开创产业新局从电动化零部件发展趋势观察,朝需求两极化→大量生产/规模经济、定制化与(少量多样)/导入市场时程缩短。电动化→电动化零部件增加,电力电子组件/模块需求成长(化合物半导体应用)。智能化→汽车电子进化,附加价值提升,异业转型。
就电动化而言,宜关注功率转换控制器发展,技术上的需求是大电压(400~900V)&大电流、热对策(功率转换)与运转效率提升,课题分别是IGBT、SiC、GaN于驱控器、SiC于直流转换器、SiC、GaN于车载充电器、直流快充椿(EVSE)、无线充电等应用。就线传技术而言,宜关注线传(油门、驾驶、转向、煞车、悬吊等)信赖度与可靠度技术应用,后续的课题是电控化与机电整合、零部件精简化与模块化与创新机构设计等。
中国汽车零部件企业长期专注零部件制造与外销,随电动化零部件需求成长,企业宜持续关注橡塑料射出成型,规画产业转型,布局电动车辆橡胶/塑料零部件,利用3D打印,替代模具、夹治具制作,缩短进入市场时程;轻质合金应用于电动车辆机会增加,高强度钢板应用与材料成本合理化是近期关切项目;复合材料或异质材料随定制化需求,将增加使用频率,成型技术与接合技术是后续关注课题。电动化零部件智能制造则可藉由自动换线与无人搬运车(AGV)、人工智能与工业物联网导入应用、次世代智能机器人与自动光学检测(AOI)—光学辨识等生产智动化,优化制造与生产效率,提升产品附加价值。