伴随着工业 4.0 的推行,“精实智能制造”逐渐着重在制造现场经验及知识的持续积累,以及汇集的标准化作业程序,正转为一种灵活因应个别客户需求、兼顾质量、成本与交期之制造策略。精实智能制造的成功案例为数仍少,产业界正面临如何冷静评估新技术的投资,特别是结合本身组织能力构建智能制造实践典型的课题。
日本 DMG 森精机引进丰田模式
柴田友厚在新出版的《发那科与英特尔之策略:机床产业 50 年的革命史》指出,森精机成立于 1948 年,初期制造纤维机械,1968 年起开始生产 NC车床,公司营运随之增长,1976 年 NC车床市占率跃居日本首位,并开始进入综合切削中心机市场,持续增长为领导型企业。后因开发出独有的计算机与操作暨人机接口系统,成为日本机床业界中最具代表性之厂商。
另外,2011 年 7 月底聘用原丰田汽车生产管理、生产技术事业群总经理,在位于三重县的主要生产据点伊贺事业所构建以装配线为主轴之丰田式生产管理,先实践在生产台数 10%,达到了省人化效果,工厂生产效率提升了 20%。零件的调配采用实时生产方式,不仅仅是减少零件库存,销售部门也可重新检视与制造部门的信息传输链接,即便是研发部门也可在短时间内快速地进行组装设计。
笔者实地考察 DMG 森精机,作者检视上述变革,有两个重要发现。
第一,装配线精实变革透过像制造现场的技术标准化,譬如“铲花”等熟练技术的训练,使网宇实体系统链接得到改善,达成生产高性能产品之目标。另一方面,2016 年伴随着与德国机床厂商 DMG 的正式合并,开始积极开发与导入智能制造,迈向重要环节之一的“数字工厂”(Digital Factory)。
第二,数字工厂以人机接口CELOS 产品组合为核心,人、机台与工厂间彼此相互连结,让直到目前为止难以被发现的信息得以可视化,从生产计划、生产准备、生产设备监控等实现数字化服务,做到预防维修保养节省成本、故障时的快速恢复运作。透过网际网络的实时通讯功能,可实时获得联网的机床稼动状况等信息,也可找出对客户端生产效能提升的改善方法。同时,透过服务中心、零件中心、解决方案中心等组织运作,有效解决客户面临的问题。

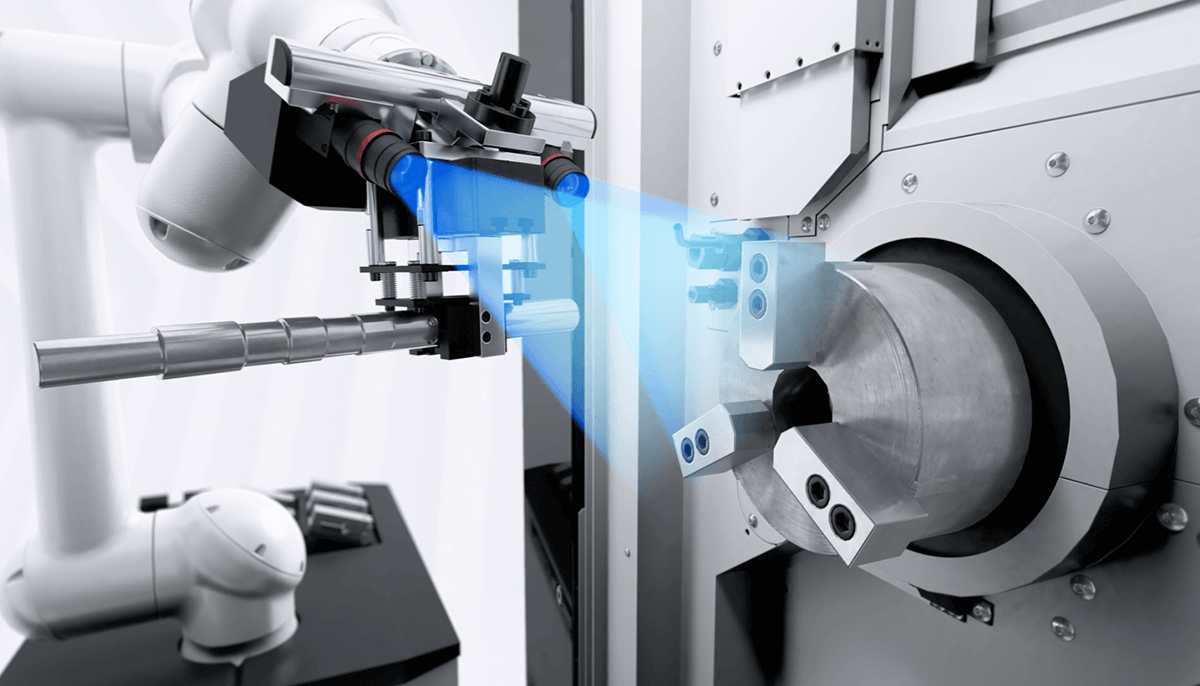
韩国现代 WIA 的精实变革与智能应用
韩国的现代WIA隶属于现代集团,是以汽车零件制造为其主要领域的国际型企业。虽然并没有直接导入丰田式生产管理,但在日韩合资公司与工厂的参观学习当中,学习到工厂的营运方法、功能别流线生产、产品别少量生产、工程别的自主检查、第三方的质量保证制度、提案改善制度、自主检查等,致力于网宇实体系统的改善推动。2000 年起结合美国的统计质量管理与日本的全面 TQM 全面质量管理,由管理职积极地参与来确保质量,而不是交由现场的
作业人员来自主管理。尤其积极导入 IT技术,以整合开发、生产与采购等基础信息系统,厚植营运组织能力。
现代 WIA 目前以智能制造平台、IRIS(Integrated Revolution of Industrial Solution) 智慧工厂解决方案的开发与推动做为营运重点。其基础系统包括 1.HW-MMS(智慧方案)2.HYUNDAI-iTROL(CNC 数控平台)、3.CNC 智能加工程序等 3 项。HW-MMS 是利用物联网,来达成实时远程监控现场机台设备,无论是从平板或 PC 或智慧手机,皆能无时无刻可确认工厂稼动情形与异常状况。还能透过总公司的服务中心来对全球客户进行远程诊断、找出问题点及预知保养。HYUNDAI-iTROL 是除了机床控制系统上的基本功能外,还具备节能功能、追踪加工履历与工厂远程控制等功能,能够记录分析运作时的能源消耗资讯,以及预知异常可能原因。智能加工流程经由对工具的监控、加工误差的最小化、电力监控等,实现了生产效率与加工精度的提升,并让客户操作更具便利性。
现代 WIA 正透过物联网连接 40 间工厂、300 台的设备,进行远程监控,达成数据收集与客户问题解决。将来以运用大数据与人工知能之通用模块、强化预知保养功能为目标。
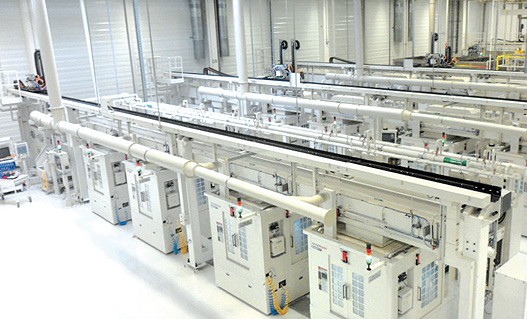
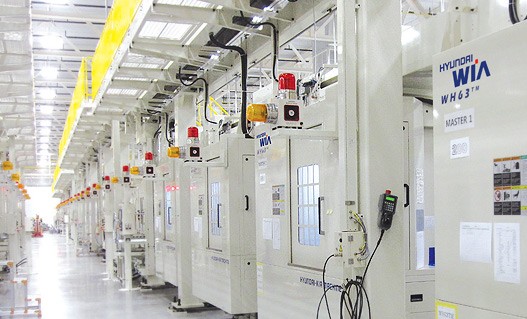
日韩精实智能制造的意义与课题
两家企业的精实智能制造有两个相同的目标:厘清本身企业组织能力;实践可视化、异常感知与预知保养。具体而言,就是透过内部生产稼动信息的实时化,有效结合客户端中自己公司产品,来实现远程监控与预知保养。前者是生产效率的提升,后者是客户解决方案的提供。
另一方面,日本企业持续以现场人员与机械的协同作业来改善网宇实体系统,达到生产效率及质量的提升目标,具备重视设备可视化与预知保养的策略导向。相对而言,韩国企业则在兼顾客户问题解决方案的同时,以打破第三次工业革命自动化基础的低效率,实现高效率智能制造为主要发展方向。
日韩企业的精实智能制造显示,贯彻装配线精实生产、致力于人与作业现场的可视化、开发客户问题的解决方案,是今后的三大课题。