文|李建、刘明星、王思杰
日本比中国更早进入老龄化社会,熟练劳动力在逐渐退出市场,为了将技艺传承下去,延长高龄员工的工作年限,以及吸引女性和年轻人加入到制造业来,日本的制造业企业正在掀起一波人工智能辅助提升效率的浪潮。
MFC《金属板材成形》正在整理日本制造业的一些企业的成功经验,分享到中国的冲压钣金行业人士,供企 业决策层参考借鉴。
LifeRobotics 公司:人与机器人协作工作,降低劳动强度
网址:www.liferobotics.com 传统工业机器人因为手肘突出,在和工人协同作业的时候容易伤到工人,该公司开发出了可伸缩关节机器人,申请了专利TRANSPANDER,动作简洁,占用空间小。
该公司开发 CORO 机器人已经十一年,已经在劳动密集型作业现场得到成功应用,例如 餐具的甄别、摆放和补缺等。
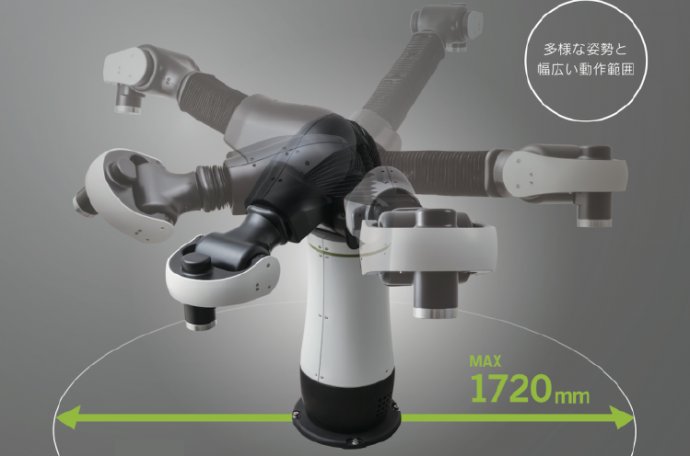
理光股份:运用 BizRobo 软件减轻白领工作,提高部门效率
网址:www.rpa-technologies.com
理光公司2016 年采用了机器人流程自动化(RPA)技术,使传统人力收集数据、输入、核对三大业务实现了自动化,削减了 55-85% 的用人工数。
PRA 不需要专门的编程技能就能定型业务自动化,在日本已经有上百家公司 引进了 4000 多套 BizRobo 技术。
理光公司导入了“单价管理登录”、“应收账款取消处理入账附加条件”等6个业务,其中单价模块的 13 步骤中有 11 个换成 RPA,时间从 3 分钟缩短到 30 秒。
应收模块每月有 35 万件请求,其中 10% 无法自动取消,需要 84 名员工来处理,目前该公司正努力实现 70% 的业务自动化,力争在 2018 年把 92 项业务,2019 年 137 项业务全部导入 PRA。
这项技术主要是来应对日本不断老龄化导致的劳动力不足的情况。
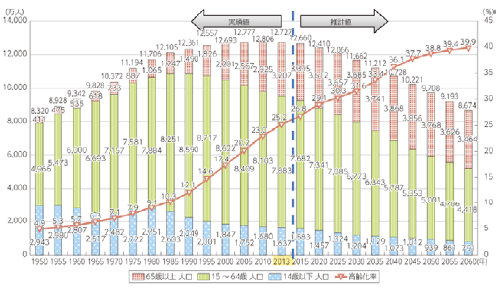
HILLTOP :完全自动化带来的人类高附加值工作转换
网址:www.hilltop21.co.jp
HILLTOP(原名山本精工,YAMAMOTO SEIKO)是一家擅长快速制作铝制品原型、零件、表面处理和夹具的中小企业,为飞机、汽车和特种车辆提供多品种、 小批量的加工服务。
该公司通过信息化技术把熟练员工的技能数据化和数字化,让全自动化的机械24小时无人生产。
生产现场几乎不要工人,大部分的作业人员是从事类似于程序员的工作,白天看图纸、构思设计、编程,然后模拟输出加工数据到机器,之后机器可以在夜间按照数据把零部件加工出来。
该公司可以实现新品五天交货,重复产品3天交货,最低接受一件加工,基本杜绝了为赶交货期日夜加班的情况。 工厂也装修得像设计工场充满活力。
该公司的工作方式改变增加了对富 有创意的年轻人的吸引力,员工人数 从 100 多人减少到 70 人左右,但是 业务扩展到了全世界,赢得了包括迪士 尼、优步这样300多家客户的订单。 Hilltop 在美国硅谷也设立的办公室,在肯塔基州开辟了生产基地,利用时差在日本开发,美国生产,实现超短交货高质量原型件的奇迹,也因此获得了巨大成功。
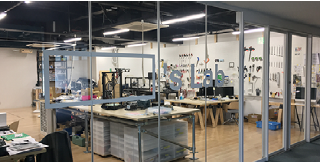
小林制作所:在现场监理生 产技术和 IT 技术结合的系统
网 址:www.kobayashi-mfg. co.jp
位于石川县的小林制作所是一家创立于1919年的企业,从事钢铝等材质 的精密钣金加工,可以定制小批量加 工几厘米到5米的钣金结构件。该公司从1980年开始,就自主研发了名为SOPAK的生产管理系统,变革了工作 方式,使效率和质量显著提升。
这套系统的特点是:1、一元化管理客户信息、交货期、材料、画面、作 业人员、作业进展、单价、成本价等制造信息。2、系统数据来源于条形码阅读的数据和在工厂按照200多台摄像机的录像数据,实现彻底的追踪管理。3、双击系统中订单名称,可以马上看到“何时何地何人进行了何种加工”的信息。仅白山市的工厂每月能接到2万份订单,涉及10万种产品,超过品种小批量生产,但是生产速度却很快。通过持续的改善,公司的生产能力提高到2012年的1.8倍。
该公司的系统通过数据记录能随时正确把握工作人员的工作方式,运用适当 的评价提高员工积极性,不是为监视员工,而是避免懈怠管理和劳动事故的发生。对于超多品类生产型,该 Sopak 系统能保证全线产品的规范化,瞬间检索出每件产品之前的生产影像记录,通过观察之前的数量工人的操作,后来的员工即使没 有手册指南也能完成同样的操作。
这套可视化系统从2012年开始也对外销售,到2017年被40多家企业引进,用来实现企业活动整体的可视化,推进工程改善、成本分析、教育训练、作业标准化。一般刚开始引入,员工是排斥的,但是体会到便利性之后,就能依赖这种协助人类工作的工具。

旭铁工(ASAHI TEKKO):低成本的物联网系统改善汽车 零部件制造企业
网址:www.asahi-tekko.co.jp 旭铁工主要服务对象是日本丰田汽车,生产各种金属加工零件,厂内的工具
机有50%的设备生产于1926~1989年,应丰田的要求开始可视化管理的尝试。该公司最初用人工计时计数的方式,调查生产线设备状况,并据以改善流程及淘汰异常设备,结果生产线的产能上升70%,不需要投资新生产线就可以满足客户需求,省下设备投资成本。
但测试中觉得过于耗费人力,所以就开始以简单的传感器计数计时。他们以只获取“最低限度的数据和初期投资维持低价”的原则从2014年开始研发。第一代系统的做法是用秋叶原买的几百日元的通用感测器,装在机器开关附近,并接上简单的三色灯,侦测设备以一定频率 运作,正常就显示绿灯,不正常就会亮黄红灯,并利用这些资料统计,确认单 一设备正常运作率,确认测量效果与人 工测量相当。
2015年开发第二代“I- 智能灯笼”系统,可将设备的运作和停止状况实时记录在通用显示器上,还是使用廉价传感器测量每个产品的循环时间。2017年已经更新到第三代,大大提升效率,并降低员工的劳动时间和假日加班出勤。
传感器透过简单的无线网路模组与路由器,连到旭铁工设立的云端系统, 由系统进行统计,确认设备运作频率, 累积一段时间的资料后,就可以统计各项设备与生产线的效率。而客户可以透过电脑或手机连上网路查询,并配合现场了解何为正常与不正常的状况后,进行各项操作。
由于成效显著,投资要求低,不仅在日本,在中国和东南亚都有庞大的需求,该公司在2016年成立i Smart Technologies公司,专门来推广他们研发这套系统。
CLIMB NCD: 金属模具智能化
网址:www.climb-ncd.co.jp
该公司创办于1988年,是一家汽车冲压模具CAD/CAM建模及加工, 以及制造工艺CG动画制作的专业公 司。
创始人高桥一直从事模具行业, 48岁感知到3D数字建模技术的潜力,辞职创办了CLIMB NCD公司,奉行 的企业理念是“规模虽小但行王道”,以极强的模具设计和制造能力,介入到整车的设计环节,获得与大企业平等对话的权力。

该公司通过3d模拟软件,为客户缩短开发时间,并且利用自己的技术优势,制造直观的模具加工过程影像让客户的员工直观使用,以及向他们的用户演示。MFC-home2的微信公共账号上有转载他们制作的精良工艺视频。
基 于CAM模拟,CLIMB NCD实现了五轴联动加工模具。该公司认为传统的评估模具企业的低成本、短交期、 高质量的标准正在受到挑战,并不足以让日本模具在世界竞争中处于优势,还必须加入物联网的智能技术。
该公司牵头成立了智能金属模具研究会,吸收了模具企业、大学、IT 供应商、自动化企业的专家,研究在模具上安装重力感应器、位置感应器等感应装置,收集数据,检测出异常,并自动停止设备运转,提供预测性维护服务。该研究会出了一些教材,并经常组织内部培训、竞赛评奖,把这些模具上的感应装置商品化销售,提高模具的附加值。
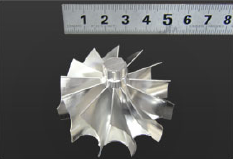
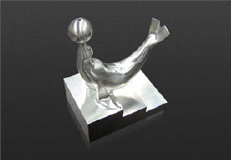
IBUKI:通过物联网和人工 智能实现新能力
www.ibki-inc.com
IBUKI(原名安田制作所)是山形县的一家中小的树脂模具生产商,其模具能生产出极具设计感和质感的纹理的零部件,在汽车行业不断增加市场份额。 在上智能化之前,该厂主要是依赖厂长的丰富经验和知识来才处理订单需求,因为精力有限,还要管理工厂和培训人才,所以业务处理的效率和质量都不理想。
2014年和OTTO咨询公司合作,谋求用物联网和人工智能来进一步提高生产效率。
模具在加工的过程是不断有损耗的,加工的零部件的精度一直变化,过去保持产品的一直性主要依赖工人的直 觉,而培养一个优秀熟练的工人需要时间和大量的试错成本。现在 IBUKI 公 司在模具内置了大量的传感器,准确的 探测树脂的流动的情况,即时通过可视化的图像检测出不合格产品,发出警报预警,避免大量不良品的产生。
除了开发监测系统之 外,IBUKI还把这些数据反馈给树脂压力机的生产商,让他们在研制设备的过程中进行优化改良。
该公司使用的是OTTO的子公司LIGHTz(http://lightz-inc.com)开发的ORINAS的人工智能技术,将熟练工人的思考和操作方式通过人工智能技术可视化,比如以流程图展示思考的过程,内置到系统中。没有经验的工人可以在30分钟内完成对过去类似情况的检索和学习,然后合格地完成任务。在没有ORINAS之前,这个学习的过程需要半天的时间。
和上述的旭铁工类似,IBUKI正在谋求从一个纯粹的模具制造企业,转型为也能提供改善工厂生产效率的服务 型企业,将在内部实现的制造知识和经验可视化的成功经验,给类似的企业提供咨询。IBUKI也开设了金属模具私塾服务,向年轻人提供传授模具知识。
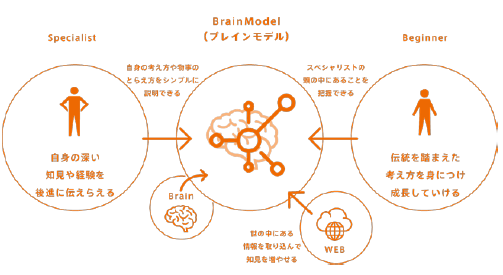
MFC金属板材成形平台
1. 官网:www.mfc-china.org
2. 今日头条:金属板材成形之家
3. 微信订阅号:MFC-home 金属板材成形之家
4. 群友通讯录:「MFC金属板材成形杂志」1.6万人通讯录
5.千聊优课:MFC-冲压联盟名家直播间