知识分享
十二年技术沉淀
SMC材料模压SMC MATERIAL IS MOLDED
做行业领导品牌
正西液压

SMC材料模压
SMC(Sheet Molding Compound,即片状模塑料)模压是指将片材按制品尺寸、形状、厚度、重量的要求裁剪下来,然后将裁剪好的材料叠合放入已加热的金属模具型腔内,按预先设定好的加压方式固化成型。
PART.1
SMC模压工艺优点

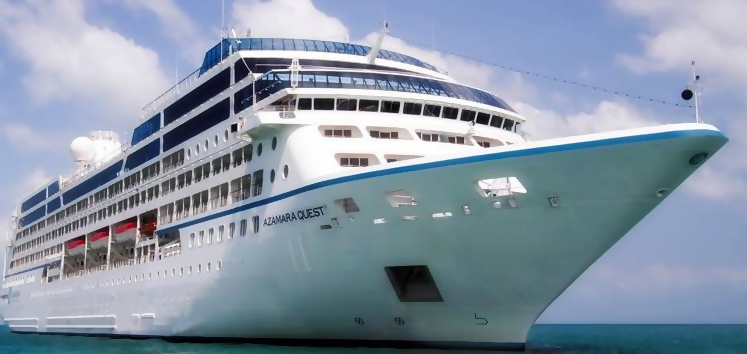
SMC材料模压工艺虽然是玻璃钢/复合材料成型工艺生产效率最高的一种,其工艺有不少的优点,譬如:制品尺寸精准、表面光洁、制品外观及尺寸重复性好、复杂结构也可一次成型、二次加工无需损坏制品等。
PART.2
常见质量问题及解决方法
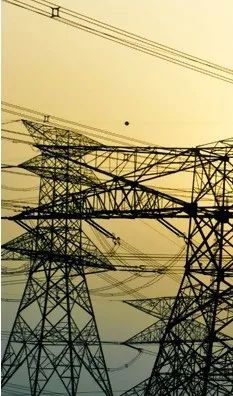
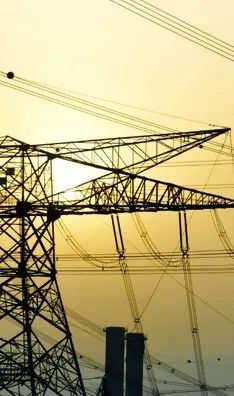
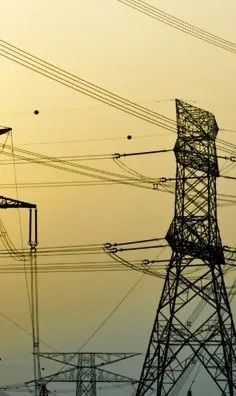
虽然SMC材料模压工艺有着许多的好处,但是在SMC模压生产过程中也会出现不良缺陷现象,主要表现以下几个方面:
PART. 2.1
缺料
SMC模压成型件没完全充满,其产生部位多集中在SMC制品的边缘,尤其是边角的根部和顶部。产生的原因及对策
01. SMC材料受热塑化后,熔粘度大,在交联固化反应完成前,没有足够的时间、压力和体积使融体充满模腔;
02. SMC模压材料存放时间过长,苯乙烯挥发过多,造成SMC模压材料的流动性能明显降低;
03. 树脂糊未浸透纤维,成型时树脂糊不能带动纤维流动而造成。由上述原因所引起的缺料,最直接的解决方法是切料时提出这些模压材料;
04. 加料量不足引起缺料。解决方法是适当增加加料量;
05. 模压料中裹有过多的空气及大量挥发物。其解决方法有:适当增加排气次数、适当加大加料面积隔一定时间清理模具、适当增大成型压力;
06. 加压过迟。模压材料在充满模腔前已完成交联固化;
07. 模温过高,交联固化反应提前,应适当降温;
PART. 2.2
气泡
模压材料固化不均和脱模后的产品收缩。产生的原因及对策
01. SMC模压材料中裹着大量空气以及挥发物含量大,排气不畅;SMC料的增稠效果不佳,不能有效的赶出气体。对于上述引起原因,可通过增加排气次数以及清理模具相结合的方法而得到有效的控制;
02. 加料面积过大,适当减少加料面积可得到控制。在实际操作中,人为因素也有可能造成砂眼,比如加压过早,有可能使模压料中的气体不能排出,造成制品表面出现气孔的表面缺陷;
PART. 2.3
翘曲变形
模压材料固化不均和脱模后的产品收缩。产生的原因及对策
在树脂固化反应过程中化学结构发生变化,引起体积收缩,固化的不均匀使得产品有向首先固化的一侧翘曲的趋势。
制品的热胀系数较大于钢模具。当制品冷却时,其单项收缩率大于模具的单项热收缩率。为此,采用以下方法加以解决:
01. 减少上、下模具温差,使温度分布尽可能均匀;
02. 使用冷却夹具限制变形;
03. 适当提高成型压力,增加制品的结构密实性,降低制品的收缩率;
04. 适当延长保温时间,消除内应力;
05. 调整SMC材料的固化收缩率;
PART. 2.4
起泡
模压材料固化不均和脱模后的产品收缩。产生的原因及对策
可能是材料固化不完全,局部温度过高或是物料中挥发物含量大,片材间因聚集空气,使制品表面的半圆形鼓起:
01. 适当提高成型压力;
02. 延长保温时间;
03. 降低模具温度;
04. 减小放料面积;
PART.3
正西液压复合材料成型液压机
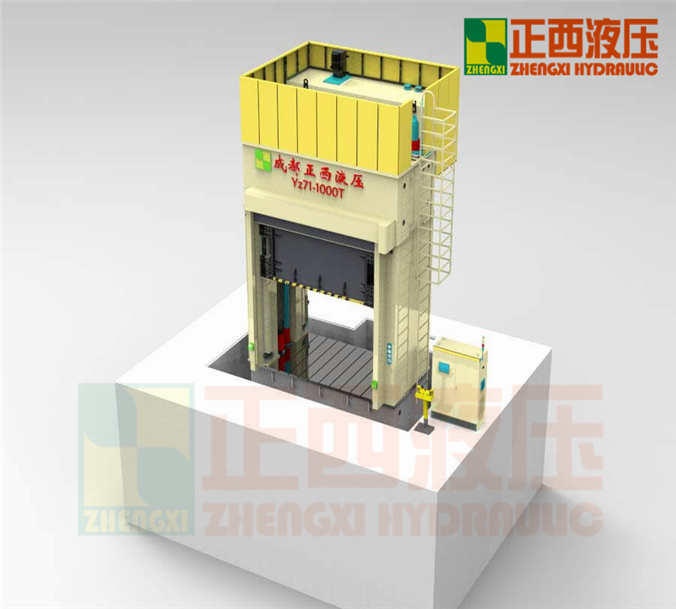
主要适用于热固性与热塑性及其他各种可塑性材料模压成型,产品尺寸及精度要求高,优先选择框架式结构;
在汽车、航空、高铁等交通行业及家居、电力行业广泛应用;性能特点
01. 框架式/四柱式结构;
02. 框架式结构刚性好,稳定性高,抗偏载能力强,调整后不宜发生精变跑偏现象;
03. 四柱式结构立柱导向,可调性强,性价比高;
04. 速度快,震动小;
05. 单独的开模缸系统化;